-
Xinxintian Industrial Zone, Shajing Street,Bao'an District, Shenzhen, China
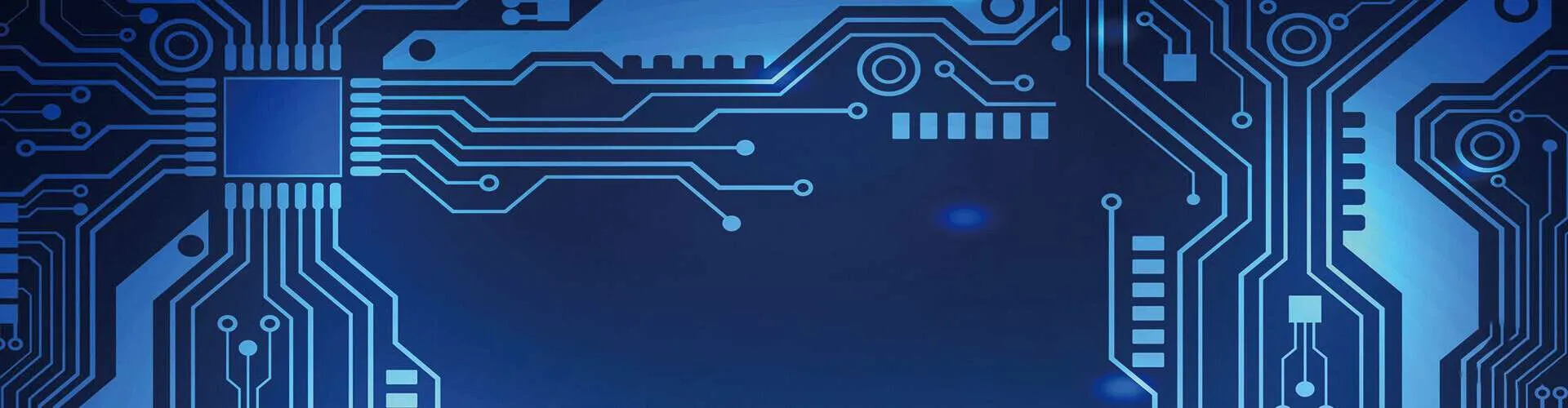
Quality Assurance Guarantee
2025 PCB assembly Quality Assurance Guarantee : Expert insights to minimize defects, boost reliability, and ensure compliance. Discover actionable strategies for production and cost savings
Quality Assurance Guarantee:
PCBA processing full process quality control
the core code for creating high-reliability electronic products
Abstract In the field of electronic manufacturing, PCBA (printed circuit board assembly) is the core link that determines product performance and reliability. This article deeply analyzes the full process quality control system, covering 11 key steps from design verification to reliability testing, combining ISO 9001 quality management standards and industry-leading processes to reveal how the head factory achieves a pass rate of more than 99.9%. Through structured control strategies and intelligent detection technologies, help companies improve product competitiveness, reduce after-sales risks, and accelerate market transformation.
I. Four dimensions of full process Quality Assurance Guarantee
1.Design verification and manufacturability optimization
• DFM (design for manufacturability) principle: optimize component layout through 3D simulation technology to ensure that the minimum component spacing is ≥0.5mm to avoid the risk of soldering bridging.
• Thermal management and EMC design: use ANSYS thermal simulation tools to analyze heat dissipation paths and disperse high-power components; reduce electromagnetic interference through SIwave signal integrity analysis.
• Standardized module library: Establish IPC-7351 standard package library, reduce the use of customized components, and shorten the production cycle by 15%.
2.Raw materials and supply chain management
• Supplier classification management: Implement AEC-Q200 certification to screen suppliers, establish VMI (supplier inventory management) mechanism, and ensure 3 months of safe inventory of key materials.
• Incoming material inspection technology:
• X-ray inspection (AXI): Identify internal solder ball defects of BGA components (detection rate>99.5%).
• LCR tester: Verify resistance/capacitance tolerance (accuracy±1%).
3.Intelligent production and process control for Quality Assurance Guarantee
• SMT process optimization:
• SMT machine precision control: Use FUJI NXT III equipment, with a mounting accuracy of ±25μm.
• Reflow soldering temperature control curve: lead-free process peak temperature 245±5℃, time 50-70 seconds, real-time monitoring through KIC temperature measurement system.
• AOI+AI defect recognition: Applying Koh Young 3D AOI equipment, combined with deep learning algorithm, the detection rate of false soldering/wrong parts is increased to 98%.
4.Full-dimensional inspection system
Inspection stage | Technical means | Key indicators |
---|---|---|
Process inspection | SPI solder paste inspection | Thickness tolerance ±10μm |
Functional test | ICT/FCT test stand | Coverage ≥95% |
Environmental test | Temperature cycle (-40℃~125℃) | 1000 cycles without failure |
Life verification | HALT high accelerated life test | MTBF≥100,000 hours |
5.1 Defective product management and continuous improvement
1. Defective product traceability and analysis
2.8D reporting mechanism : Conduct root cause analysis (RCA) of batch defective products, such as locating welding temperature fluctuation problems through SPC data.
3.Improvement closed loop : Feedback the analysis results to the design and process departments and update the work instructions (SOP).
5.2 Continuous improvement (Kaizen)
- Hold quality meetings every month to optimize processes (such as “SPC application” in the knowledge base [12]).
- Introduce AI predictive maintenance to reduce production fluctuations caused by equipment failures.
6. Construction of quality management system
6.1 Quality policy and objectives
- Set a “zero defect” goal and include the pass rate in the department’s KPI assessment (knowledge base [12]).
6.2 Training and certification
- Regularly conduct ESD protection and IPC standard training (“Electrostatic protection rules” in the knowledge base [2]).
Obtain ISO 9001, ISO 13485 and other certifications to enhance customer trust.
Five strategies to improve market conversion rate
Data-driven quality traceability • Establish an MES system to achieve full-link traceability from material batches to finished products, and shorten the time to locate quality problems by 80%.
Customer customization services • Provide PCBA OEM + full BOM procurement services, and support small batch quick response (72-hour delivery).
Visual quality report • Automatically generate IPC-A-610G standard report, including X-ray slice diagram and SPC process capability analysis (CPK≥1.67).
Certification system endorsement • Pass IATF 16949 (automotive electronics) and ISO 13485 (medical equipment) certification to expand high-value markets.
Cost optimization solution • Solder joint reliability improvement technology: Through IMC (intermetallic compound) thickness control (2-5μm), reduce the rework rate by 30%.
Industry authoritative external links and standard references • International standards: IPC-A-610 Electronic Assembly Acceptance Standard | ISO 9001 Quality Management System
• Detection technology: Keysight ICT Solution | Nordson DAGE X-ray Detection
• Industry white paper: 2024 Global Electronic Manufacturing Quality Trend Report
FAQ: 6 key issues that customers are most concerned
Q1: How to ensure the long-term supply stability of components?
Through AVL (Qualified Supplier List) dynamic management, establish a dual-source procurement strategy, and reserve ≥ 3 suppliers for key materials.
Q2: Can small batch orders meet consistency requirements?
Adopting the NPI (new product introduction) process, through Golden Sample comparison and DOE experimental design, the CPK value of 50pcs order can still be maintained ≥1.33.
Q3: How to deal with the challenge of high-density PCB assembly?
Applying 01005 component mounting process and selective wave soldering technology, the minimum pad spacing is 0.2mm, and the yield is ≥99%.
Q4: How to ensure the coverage of functional tests?
Developing a PXIe architecture test platform to support parallel testing and fault injection, the typical coverage rate is increased from 85% to 98%.
Q5: Is there a special plan for dealing with humid environments?
Implementing the J-STD-033B standard, the MSD humidity-sensitive component is mounted within 8 hours after opening, and the thickness of the three-conformal paint coating is 20-50μm.
Q6: How to shorten the new product verification cycle?
Adopting the DFR (reliability design) method, 80% of potential failure modes are identified in advance through FMEA analysis, and the verification cycle is compressed by 40%.
Summary
PCBA quality control has evolved from a single production test to a full ecosystem covering design-supply chain-manufacturing-service.all work for Quality Assurance GuaranteeLeading companies have controlled the market complaint rate to ≤50PPM through intelligent equipment investment (such as investment accounting for more than 35% of the total production line cost) and data closed-loop management. Under the trend of Industry 4.0, the integration of digital twins and predictive maintenance technology will become the core battlefield of the next generation of quality management,the purpose is Quality Assurance Guarantee