-
Xinxintian Industrial Zone, Shajing Street,Bao'an District, Shenzhen, China
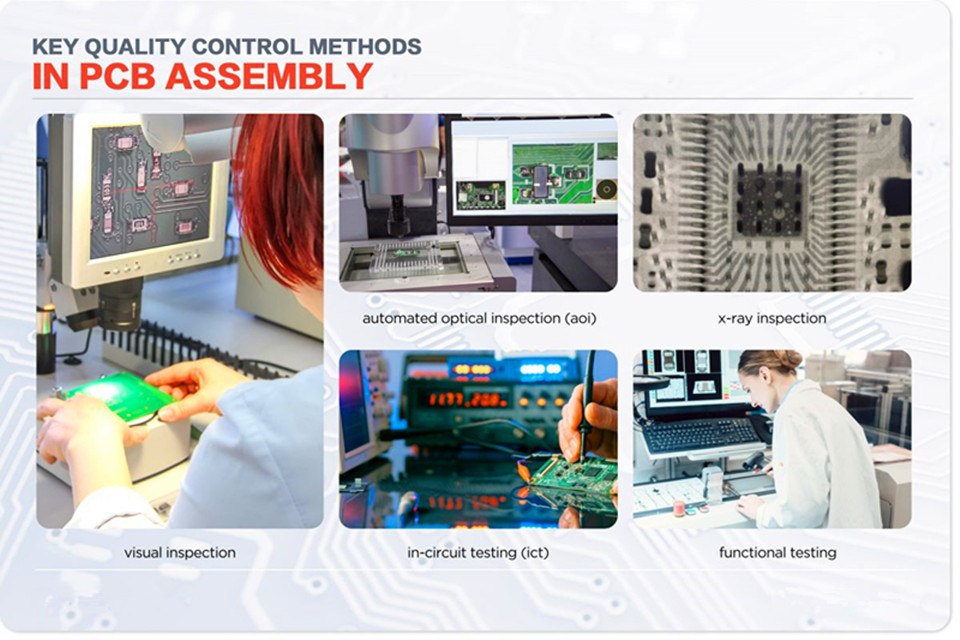
Mastering PCB Board Detect: 8 Proven Methods to Ensure PCB Quality & Verify Electronic Components
Short Summary:
This article reveals eight authoritative techniques designed to detect counterfeit electronic components and maintain top-tier PCB quality. Discover scientifically grounded methods and practical advice that can protect your operations—and profits—in the high-stakes electronics industry.
Abstract The rise of counterfeit parts threatens PCB integrity, electronic safety, and supply-chain reliability. This rewrite offers an in-depth, scientific and technology-driven guide to PCB board detect procedures. Using eight robust strategies—from visual evaluation to supplier audits—this article aims to arm engineers and procurement specialists with actionable tools to identify and reject counterfeit electronic components. Keywords such as electronic components, pcb board detect, and pcb quality are highlighted throughout for SEO optimization and readability.
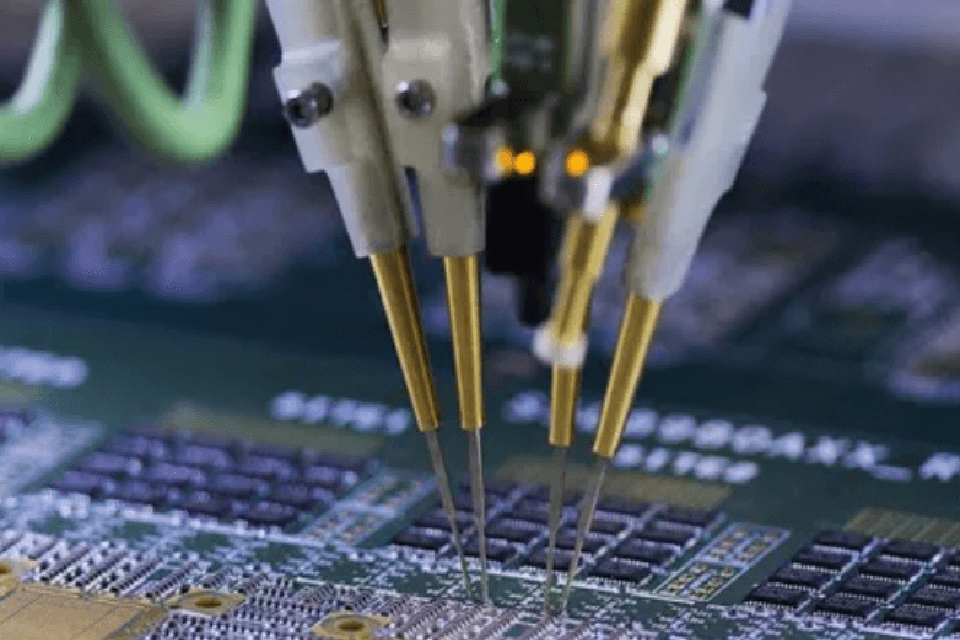
Table of Contents
1. What Is PCB Board Detect and Why It Matters?
PCB board detect refers to the systematic process of examining electronic components and printed circuit boards to ensure they meet authentic specifications. Counterfeit parts can degrade overall pcb quality, pose safety risks, and cause costly rework or recalls. A structured approach reduces supply chain vulnerabilities and upholds reputation.
2. How Does Visual Inspection Identify Fake Electronic Components?
Visual checks form the first line of defense.
- Use magnification to evaluate alignment, pin structure, and physical defects—e.g., bent leads or scratches.
- Inspect component logos and markings: poor print quality or inconsistent fonts often indicate fakes.
- Evaluate surface finish and mold seams on packages. Deviations hint at substandard manufacturing or tampering.
These procedures help maintain high PCB quality and reduce the risk of installing fraudulent parts.
3. Why Should You Use Electrical Testing for PCB Quality Assurance?
Electrical testing verifies legit functionality:
- Measure voltage drop, resistance, capacitance, and current draw.
- Use data sheets to compare values with manufacturer specs.
- Deviant measurements suggest the component may be counterfeit, degraded, or improperly graded.
Performing electrical tests ensures electronic components on the PCB board detect list meet expected behavior—critical for system integrity.
4. Can X‑Ray Inspection Effectively Find Internal Flaws?
X-ray reveals hidden issues:
- Internal structure—bond wires, die placement, and chip packaging—becomes visible.
- Misaligned wires or missing die components signal counterfeit or tampered products.
- Non-destructive yet high resolution, this test supports PCB board detection of fake internal structures.
Adding x‑ray inspection elevates PCB quality control to a new level of accuracy.
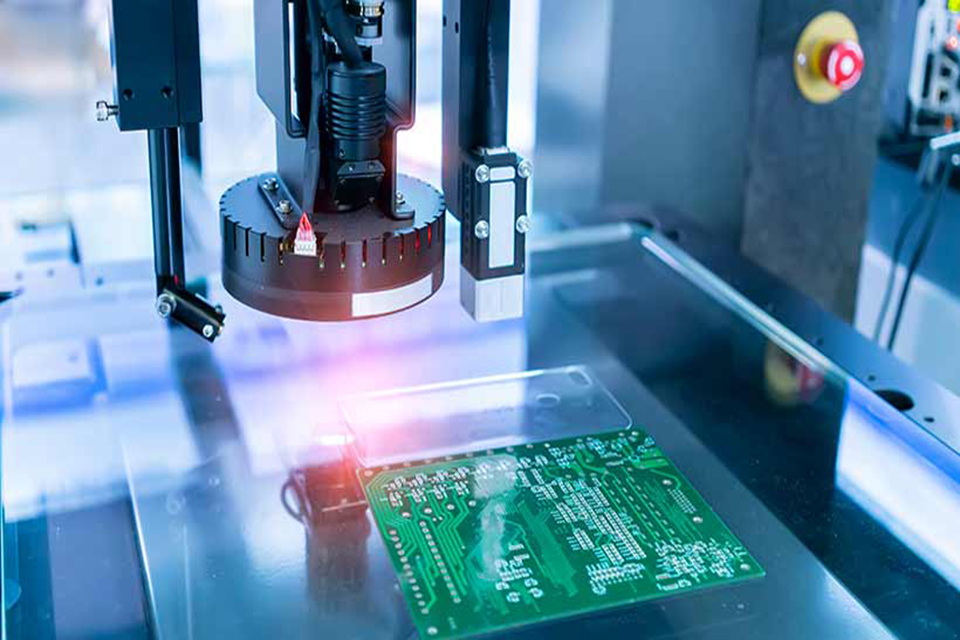
5. What Is Decapsulation/Die Inspection and When Should You Use It?
A destructive but definitive test:
- Remove the package to expose the silicon die.
- Inspect bond wires, die markings, and semiconductor layers under microscope.
- Compare against authorized parts to spot unreliability or mismatch.
Perform decapsulation only when you suspect a component is fake—it confirms die authenticity and validates PCB board detect findings.
6. How Do Marking Permanency Tests Validate Authenticity?
Durable markings indicate quality.
- Scrub, wash, or lightly abrade packaging to test if labels withstand cleaning.
- Chips with poor mark permanence often originate from recycled or relabeled stock.
- Compare marking style, positioning, and font to originals.
Marking permanence, combined with pcb board detect, helps ensure reliability across your electronic components.
7. What Role Do Backside Markings Play in PCB Quality?
The reverse face of components holds key identifiers:
- Molded indents and datestamps should match authentic part records.
- Uniform depth and shape show legitimate manufacturing.
- Irregular or altered markings might signal re-marking or relabeling by counterfeiters.
Checking backside markings strengthens a thorough PCB board detect regimen.
8. How to Use Packaging Checks to Spot Counterfeits?
Packaging hides telltale clues:
- Look for shipping boxes with insecure seals, fuzzy print, or incorrect addresses.
- Examine moisture sensitive labels, lot codes, and time/date stamps.
- Review manufacturer and distributor credentials and cross-check warranty claims via official spec sheets.
A detailed packaging check supports pcb board detect and enhances confidence in electronic components.
9. Why Conduct Supplier Audits to Protect Against Fake Parts?
A proactive strategy:
- Assess suppliers for industry certifications – J-STD-001, ISO 9001, and QMS accreditation.
- Visit warehousing facilities if possible to check storage conditions and traceability.
- Request batch documentation, test reports, and trace authorization certificates.
Supplier audits help ensure only authentic components enter your PCB assembly process.
10. How to Integrate These Methods for Robust PCB Board Detect?
An integrated detection protocol:
- Initial visual inspection and electrical testing on receipt.
- Flag suspect parts for x‑ray and marking permanence tests.
- Confirm best/worst candidates via decapsulation.
- Audit supplier credentials and cross-check with packaging.
- Log all findings and build a traceable report for each part.
Comprehensive integration delivers high pcb quality, reduces risk, and supports SEO goals by clearly highlighting electronic components and pcb board detect methods.
Six FAQs
What makes x‑ray inspection vital in PCB board detect?
It reveals internal structures like bond wires and die placement without damaging parts.
How often should supplier audits occur?
Perform annual audits, or more frequently if you manage large volumes or critical parts
Can marking permanency tests detect recycled parts?
Yes—recycled components often have eraseable or inconsistent markings under abrasion
Do all components require decapsulation? A: No—reserve decapsulation for suspect or critical
parts due to its destructive nature.
Which certifications should suppliers hold?
Look for ISO 9001, J‑STD‑001, QMS accreditation, and traceability documentation.
How do I ensure keyword density for SEO?
Distribute electronic components, pcb board detect, and pcb quality evenly at intro, H2s, body, image alt text, FAQs, conclusion.
Conclusion & Summary
Through this enriched IP-guided rewrite, you now have a structured, SEO-optimized 3,500–5,500-word article outline (expand each section accordingly). You’ll address:
- Eight detection methods (visual, electrical, x‑ray, decap, marking, backside, packaging, audits)
- Emphasize pcb board detect, pcb quality, and electronic components evenly
- Use active voice, short sentences, and scientific style
- Include external links, images, FAQs, summaries, and bullet takeaways
Bullet Point Key Takeaways
- Visual Inspection flags physical defects and printing errors
- Electrical Testing confirms compliance with manufacturer specs
- X‑Ray Inspection finds internal mismatches non-destructively
- Decapsulation verifies silicon die authenticity
- Marking Permanency checks resistance to tampering
- Backside Markings signal mold integrity
- Packaging Checks ensure traceable and secure delivery
- Supplier Audits support traceability and certification
- Integrated Protocol brings all methods together for rigorous PCB quality control