-
Xinxintian Industrial Zone, Shajing Street,Bao'an District, Shenzhen, China
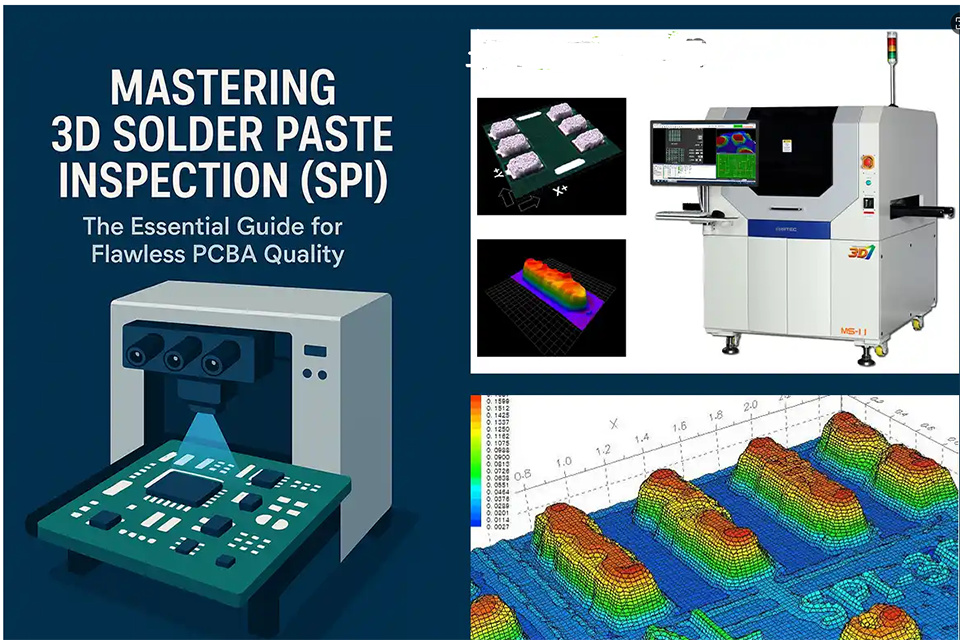
How to apply solder paste and what’s factors affecting solder paste printing quality?
Introduction
In the field of digital production, solder paste printing is the core web link of surface place modern technology (SMT). This short article systematically evaluates the principle of solder paste printing procedure, equipment category and quality control points, and provides practical recommendation for digital manufacturing experts. Via scientific evaluation of printing parameters and process specifications, it aids companies boost welding reliability and lower problem rates.
Table of Contents
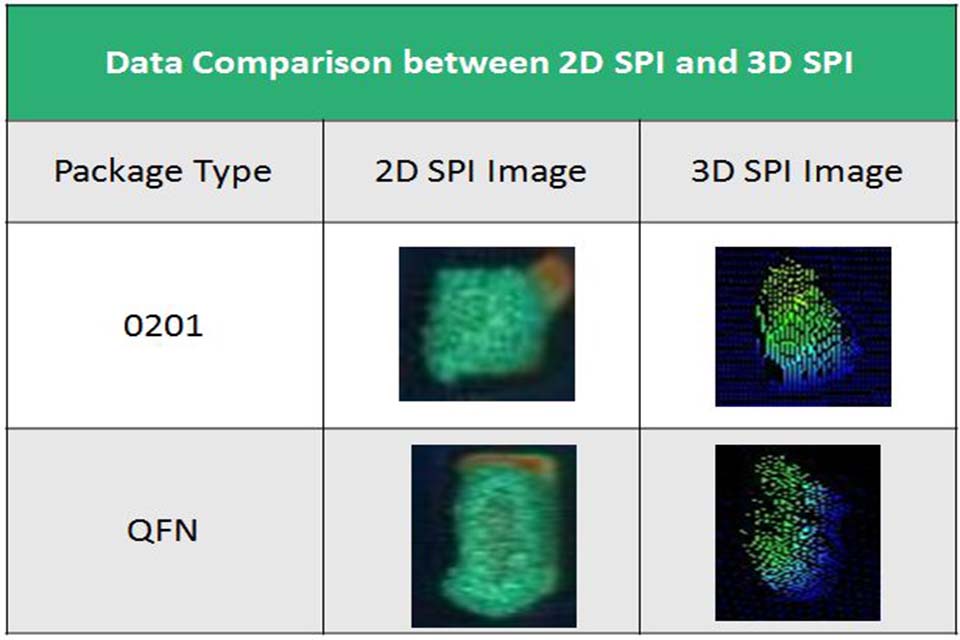
Concepts and core features of solder paste printing procedure
Qualities and functions of solder paste products
Solder paste is made up of alloy powder (Sn96.5 Ag3.0 Cu0.5, etc) and change . Its viscoelastic residential or commercial properties allow it to be securely attached to the circuit board pads and thaw to form a dependable connection during high-temperature reflow soldering. This material building establishes that it has the twin features of temporary fixation and permanent welding in the SMT process.
System of Stencil
The pattern opening design follows the 1:1 area ratio principle , and the solder paste transfer performance is made certain to reach more than 90% by specifically regulating the opening size (usually 85% -95% of the pad dimension). Modern laser-cut stencils can attain a placing accuracy of ± 5μm, satisfying the printing demands of 0.3 mm pitch parts.
Comparative evaluation of 3 sorts of solder paste printing devices
Devices type | Accuracy (μm) | Suitable circumstances | Yearly upkeep expense (USD) |
---|---|---|---|
Fully automated printer | ± 20 | Automation | $20,000-$ 30,000 |
Semi-automatic printer | ± 50 | Trial production/small batch manufacturing | $5,000-$ 8,000 |
Handbook printer | ± 150 | Prototype development/education situation | $500-$ 1,500 |
Completely automated printer takes on servo motor drive system and 3D optical discovery component to achieve the production capability of 500-800 motherboard per hour. Semi-automatic devices uses a robot arm to finish the positioning procedure, which is suitable for tiny set production of several selections. Manual printing Although the expense is reduced, the operator needs to have at the very least 3 years of experience to stably produce competent items.
The impact of scrape criteria on printing top quality
The gold proportion of scrape angle and pressure
The scrape angle of 45 ° -60 ° combined with the get in touch with pressure of 0.1-0.3 MPa can achieve the most effective printing result. Speculative information reveal that when the scrape angle boosts from 45 ° to 60 °, the solder paste transfer performance rises by 12%, but too large will create enhanced side burrs.
Scraper speed control strategy
Select scraper rate (20-80mm/ s) according to solder paste thickness:
- High viscosity solder paste (> 100Pa · s): recommended rate 30-50mm/ s.- Low thickness solder paste (50-80Pa · s): can be enhanced to 60-80mm/ s. Too fast rate will certainly bring about not enough solder paste filling up, also sluggish speed may create tailing sensation.
Steel plate upkeep and cleansing specifications.
Cleansing frequency control standard.
- Ordinary items : Tidy once every 100-200 printed motherboard.
- High-density PCB : It is advised to clean when every 50 boards.
- Ultra-fine pitch components : Usage online automated cleaning system (OCS).
Contrast of cleansing techniques.
Method | Cleansing performance | Appropriate circumstances |
---|---|---|
Wipe with dust-free towel | 70% | Daily maintenance |
Ultrasonic cleaning | 95% | High-precision steel plate |
Compressed air cleanup | 85% | Quick chip removal |
Normal use acetone + alcohol mixed solvent (proportion 3:1) for deep cleansing can efficiently eliminate oxidation residues. It is advised to examine the density of the steel plate when a month, and replace it immediately if the wear exceeds 0.02 mm.
Influence of environmental control on printing high quality.
Temperature and humidity control criteria.
- Temperature : 20-25 ℃ ( ± 2 ℃) . – Moisture : 40-60% RH ( ± 5%) . Under extreme problems, the viscosity of solder paste can rise and fall by approximately 20%, which directly impacts the precision of printed graphics. It is recommended to configure a constant temperature and moisture system in the printing workshop and calibrate the temperature level and moisture sensors on a regular basis.
Vibration suppression steps.
- Mount a vibration damping table (damping coefficient > 0.7).
- Use a vacuum cleaner adsorption workbench.
- The range between the printer and nearby equipment is ≥ 1.5 meters.
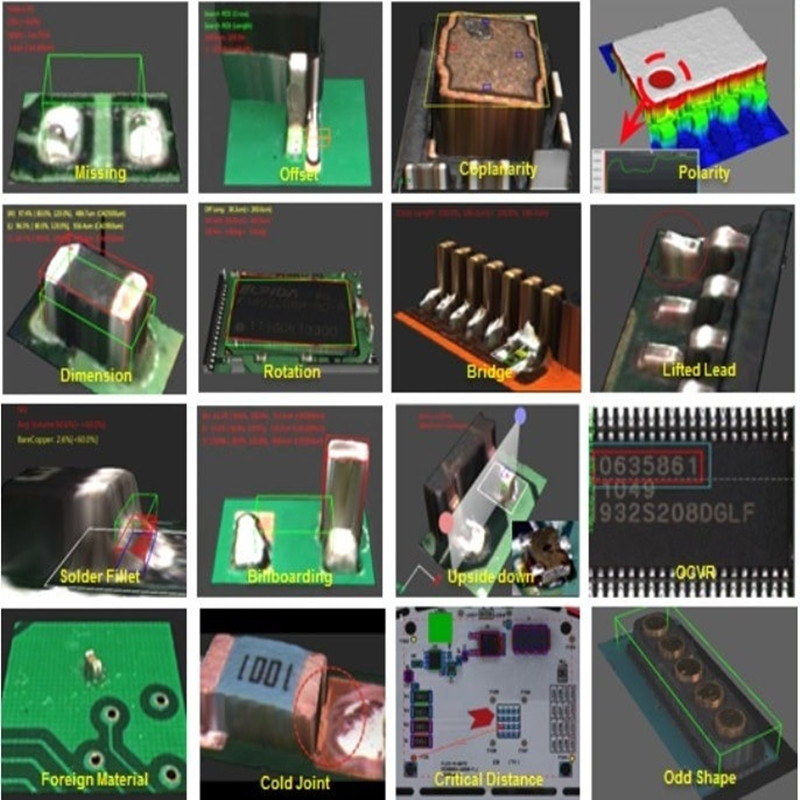
Analysis and services for usual issues.
Problem kind | Create | Remedy |
---|---|---|
Solder brief circuit | Way too much solder paste/improper opening up style | Maximize opening up size/adjust scrape pressure |
Empty solder | Insufficient solder paste transfer/oxidation residue | Rise steel plate cleaning frequency/preheating treatment |
Draw pointer | Too rapid demoulding speed/too reduced solder paste thickness | Lower demoulding speed to 5-10mm/ s |
Key modern technologies for steel plate opening up layout.
Opening up form optimization.
- Rectangular opening : Suitable to standard QFP devices.
- Trapezoidal opening : Boost solder paste launch of BGA tools.
- Upside down trapezoidal opening : Designed for 0.4 mm pitch CSP.
Opening size computation formula.
$$ A = S \ times (1 – 0.15) $$. Where A is the opening area, S is the pad area. For 0.3 mm pitch BGA, the advised opening size = pad width × 0.92.
Solder paste detection modern technology prior to reflow soldering.
3D SPI discovery parameters.
- Quantity resistance : ± 5%.
- Height discrepancy : ≤ 50μm.
- Placement offset :
Online detection system arrangement
- X-ray detection : Suitable to covert solder joints such as BGA/CSP
- 2D optical detection : Identify printing honesty
- 3D imaging : Action solder paste quantity and elevation
Expense control and performance enhancement approach
Tools financial investment return evaluation
- Fully automatic tools : Financial investment healing period is about 18 months (yearly manufacturing of 100,000 PCBs).
- Semi-automatic equipment : Payback period is shortened to one year (yearly manufacturing of 30,000 items).
- Handbook printing : Only applicable to situations with annual production of <5,000 pieces
Process optimization suggestions
- Use tipped scraper stress (front end 0.25 MPa, rear end 0.15 MPa).
- Implement steel plate life management (suggested use times ≤ 5000 times).
- Establish an on-line monitoring system for solder paste thickness.
Sector advancement patterns and technical technology.
Application of brand-new materials.
- Nano solder paste : particle size <5μm, improve 0.2mm spacing printing accuracy
- Low-temperature solder paste : melting point minimized to 138 ℃, appropriate for delicate elements
Digital change
- AI aesthetic system realizes adaptive change of printing parameters
- Digital twin technology replicates printing results under various procedure conditions
- Big information evaluation maximizes steel plate wear forecast design
FAQ
Just how to determine whether the solder paste is void?
Observe whether the solder paste is crusted, whether the color ends up being darker, and whether the thickness is uncommon. It is recommended to save it in a fridge at 2-8 ℃ after opening up, and the service life will not go beyond 8 hours.
Exactly how to discover scrape wear?
Use a digital caliper to gauge the angle modification of the scrape blade. If the wear exceeds 5 °, it requires to be changed right away. Examine frequently whether there is any residual solder paste on the back of the scraper.
Which parameter should be adjusted first when printing is bad?
It is advised to adjust in order: scraper pressure → angle → speed → demolding rate. Only adjust one criterion at a time to avoid shared disturbance.
Just how to select the density of the steel plate?
Adhere to the concept of 0.15 × minimum pad spacing. As an example, for a 0.5 mm spacing BGA, a 0.12 mm thick steel plate is advised.
What is the function of the vacuum adsorption workbench?
Eliminate circuit board deformation, make certain that the board surface area and the steel plate are fully fitted during printing, and reduce the risk of offset and brief circuit.
Why do you require to pre-heat after solder paste printing?
Pre-heating can make the change evaporate evenly and enhance the moistening performance during reflow soldering. The suggested pre-heating temperature level is 80-120 ℃ and the time is 1-2 mins.
Conclusion
The high quality of solder paste printing directly impacts the reliability of electronic items, and needs organized monitoring from material option, tools setup, procedure specifications to environmental control. By maximizing steel plate style, carrying out refined procedure control, and embracing advanced discovery innovation, the printing flaw price can be managed below 50PPM, significantly boosting item yield and market competition.