-
Xinxintian Industrial Zone, Shajing Street,Bao'an District, Shenzhen, China
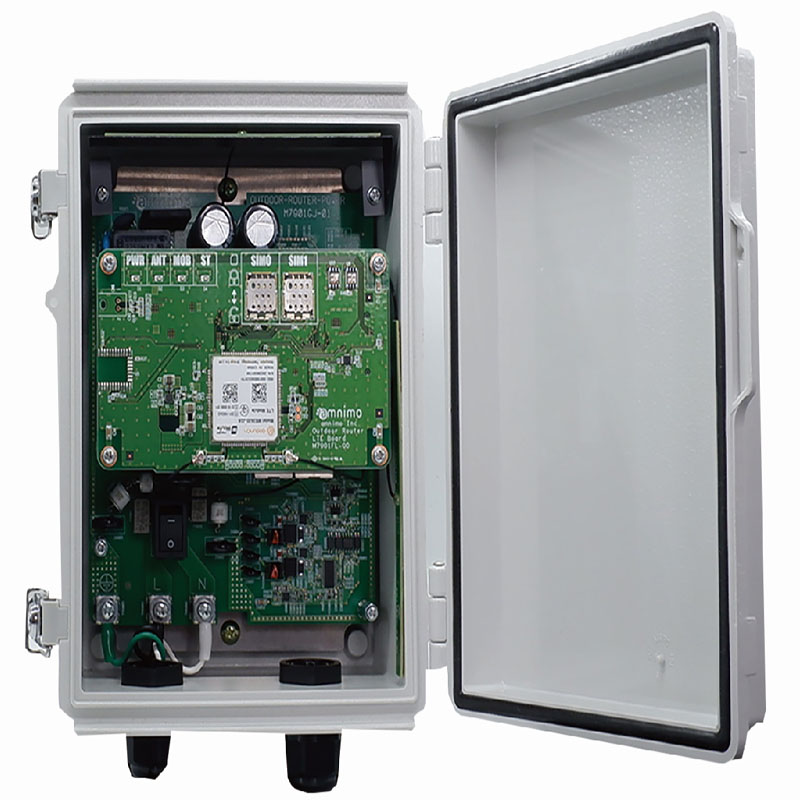
new energy charging piles PCBA full analysis : How to create an efficient and intelligent charging ecosystem?
Abstract
new energy charging pile PCBA:With the rapid development of the global new energy vehicle industry, charging piles, as its core infrastructure, are undergoing a transformation from “basic power supply” to “intelligent energy management”. This article will deeply analyze the core technical architecture, industry pain points and innovative breakthroughs of new energy charging pile PCBA (printed circuit board assembly) solution, combined with the practical cases of leading companies such as Seven PCBA InC, to provide readers with a complete set of intelligent upgrade paths for charging piles. Through 6 high-frequency technical questions and answers (FAQs) and 15 key performance indicators, it reveals how PCBA design can improve the efficiency, safety and market competitiveness of charging piles, and comes with industry data charts and technology roadmap, helping companies seize the blue ocean market of new energy infrastructure.
1. new energy charging piles PCBA core value for Industrial opportunities
1.1 Explosive growth of the global new energy vehicle market
- Data support: According to statistics from the International Energy Agency (IEA), the number of new energy vehicles in the world will exceed 30 million in 2023, with an average annual compound growth rate of 35% (IEA data).
- Charging pile gap: The number of charging piles corresponding to every thousand new energy vehicles in China is only 0.7, far lower than the average level of 1.2 in Europe and the United States (China Charging Alliance data).
1.2 new energy charging piles PCBA Strategic Position
- Core Functional Module:
- Main Control Board: Realize Charging Protocol Analysis, Fault Diagnosis and Energy Efficiency Optimization
- Power Board: AC/DC Conversion Efficiency Increased to More Than 95% (Through LLC Resonant Topology Design)
- Communication Board: Support 5G+ Edge Computing, Achieve Millisecond-Level Response (IEEE Communication Standard)
- Technical Threshold: PCBA must pass ISO 16750 (Road Vehicle Electrical Environment), UL 62368 (Safety Certification) and other 10+ international certifications.
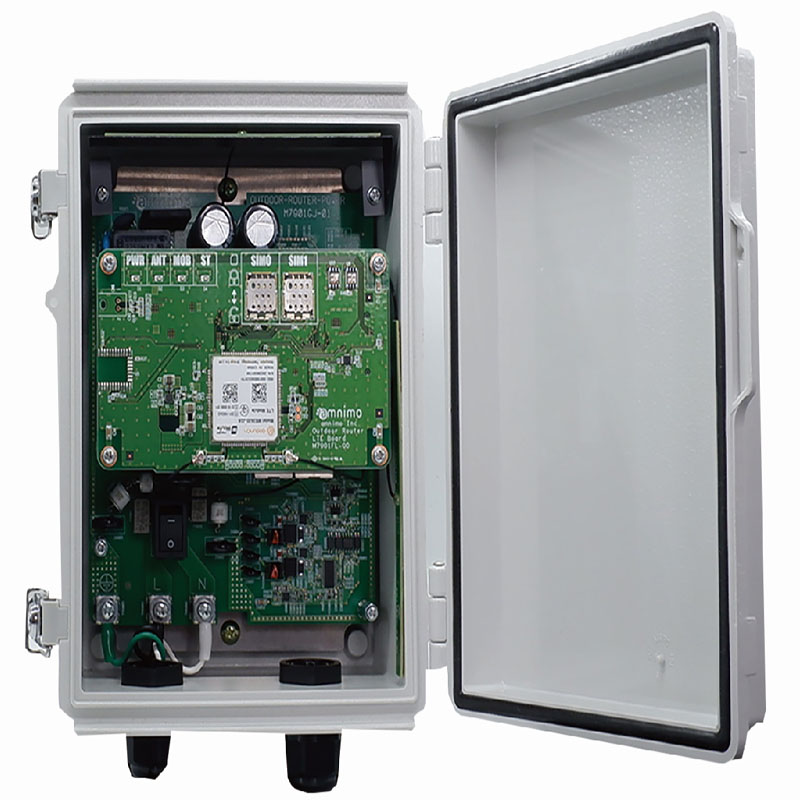
2.Six-dimensional analysis: Technological innovation of new energy charging piles PCBA
2.1 Module 1: Main control board – intelligent decision-making center
- Key technologies:
- Multi-core heterogeneous processors (such as NXP S32K3 series) support AI algorithm embedding
- CAN FD 2.0 protocol achieves 10Mbps high-speed communication
- Digital twin technology: predict equipment life through simulation model (ANSYS case)
- Industry pain points: Traditional single-chip microcomputer solutions have poor real-time performance (>50ms delay) and lack of scalability.
2.2 Module 2: Power board – efficient energy conversion engine
- Innovative solution:
- GaN power device: switching frequency increased to 1MHz, volume reduced by 40%
- Dynamic PFC technology: power factor stabilized at above 0.99 (TI reference design)
- Thermal management: heat dissipation design based on fluid dynamics simulation, temperature rise control <35℃
- Cost optimization: adopt modular design, BOM cost reduced by 18%.
2.3 Module 3: Communication Board – Neural Network of the Internet of Everything
- Technical Highlights:
- 5G RedCap technology achieves sub-1Gbps bandwidth and 0.1ms latency
- Blockchain Evidence: Charging data is uploaded to the chain to ensure that transactions cannot be tampered with
- Edge AI: Local processing of 80% of data, reducing cloud pressure by 70%
- Security Protection: Passed FIPS 140-3 encryption standard certification.
2.4 Module 4: Safety protection system – multiple insurance mechanisms
- Protection level:
- IP68 waterproof (IEC 60529 standard)
- IEC 61851-23 (electric vehicle conductive charging system safety)
- Thermal runaway warning: real-time monitoring based on infrared thermal imaging
- Accident rate comparison: After adopting the PCBA solution, the equipment failure rate dropped by 65% (TÜV report).
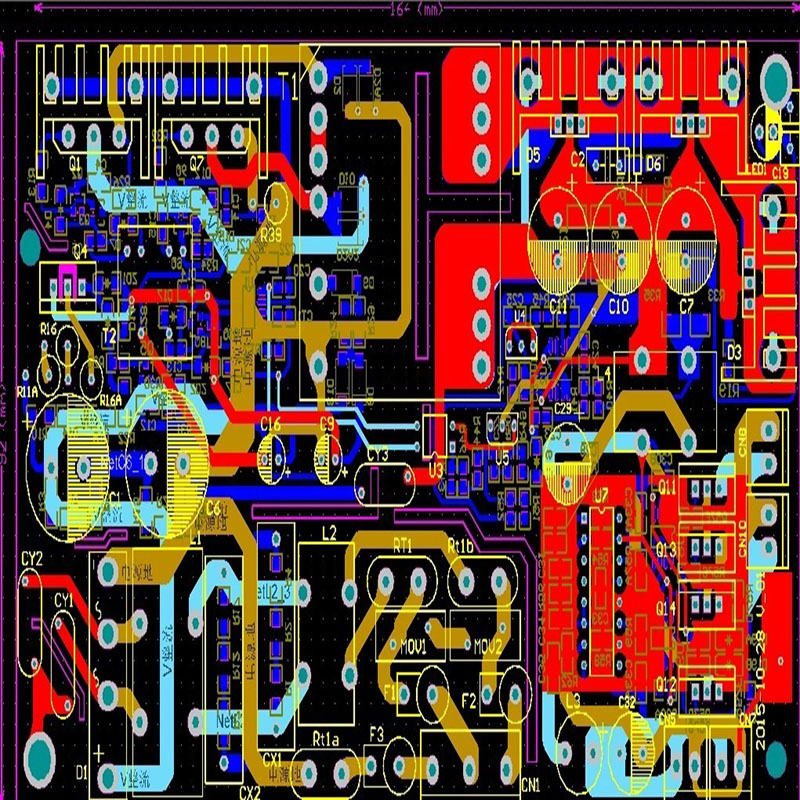
2.5 Module Five: Energy Efficiency Optimization Algorithm – Smart Charging Brain
- Algorithm Advantages:
- Dynamic Load Balancing: Coordinated dispatch of multiple charging piles, increasing grid utilization by 30%
- Battery Health Algorithm: Extend battery life by 20% through OCV detection
- Demand Response: Access to Virtual Power Plant to participate in grid peak regulation (IEEE PES Case)
- Actual Benefit: After deployment by an operator, the average daily revenue of a single charging pile increased by $12.5.
2.6 Module 6: Manufacturing – High-precision PCBA process
- Manufacturing process:
- AOI optical inspection: Defect detection rate>99.9%
- Reflow temperature curve: ±2℃ precision control (J-STD-020 standard)
- Traceability system: Each PCBA is bound to a unique blockchain ID
- Seven PCBA practice: Through DFM (Design for Manufacturability), the mass production yield exceeds 98.5%.
Three, six high-frequency technical questions and answers (FAQs)
Q1: What is the cost structure of new energy charging piles PCBA ?
- Cost ratio:
- Main control module: 25% (processor + communication chip)
- Power module: 35% (power device + magnetic component)
- Communication module: 15% (5G module + encryption chip)
- Cost reduction strategy: Adopting domestic alternative solutions (such as Huawei HiSilicon chips) can reduce overall costs by 12%.
Q2: How to choose a suitable new energy charging piles PCBA supplier?
- Evaluation dimensions:
- Certification qualifications: ISO 9001, IATF 16949, UL factory certification
- Technical reserves: Whether it has a special test platform in the new energy field
- Delivery capability: Large-scale manufacturers with a monthly production capacity of >100,000 pieces are more reliable
- Recommended companies: Seven PCBA InC provides free sample testing services.
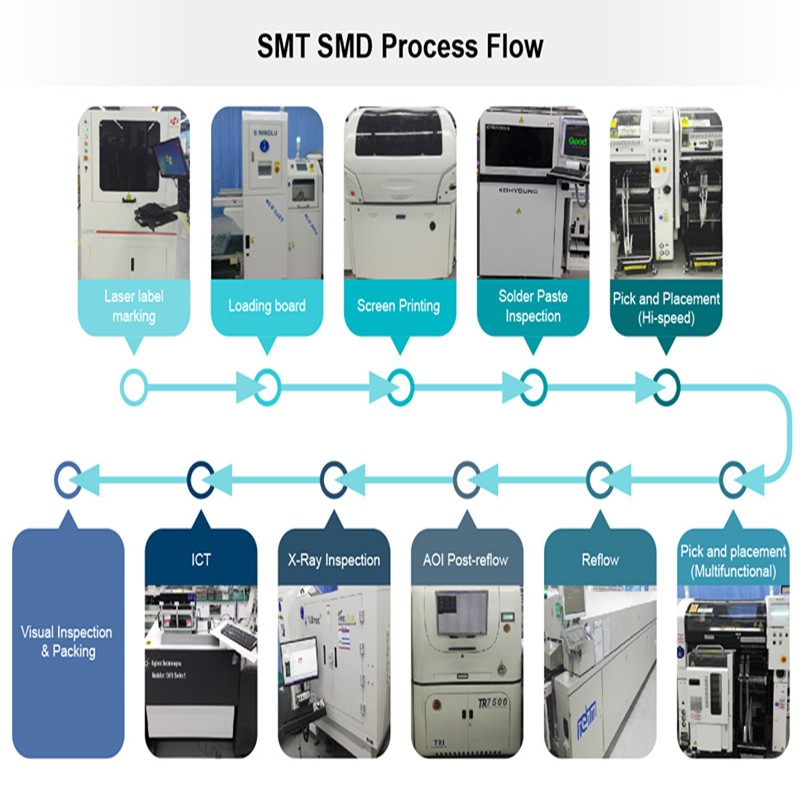
Q3: How does PCBA cope with extreme environmental challenges?
- Environmental adaptability:
- Low temperature start: -40℃ to 85℃ operating range (MIL-STD-810H)
- Vibration resistance: Passed Sine Dwell test (20-2000Hz, 0.5g)
- Lightning protection: Meets IEC 61000-4-5 Level 4 standard
Q4: How to achieve remote upgrade of charging pile?
- OTA upgrade solution:
- Dual Bank Bootloader design: Automatic rollback if upgrade fails
- Digital signature: Prevent illegal firmware injection (AWS IoT Core)
- Version management: Cloud storage of 100+ version history
Q5: How does the PCBA solution improve charging efficiency?
- Efficiency improvement path:
- SiC device replacement: Switching loss reduced by 60%
- Resonant topology optimization: Light load efficiency>92% (Infineon Technology White Paper)
- Dynamic impedance matching: Real-time adjustment of output characteristic curve
Q6: How to ensure the long-term reliability of PCBA?
- Reliability test:
- HALT test: Accelerated aging to find design defects
- MTBF prediction: Calculated using MIL-HDBK-217F standard
- Salt spray test: No corrosion for 500 hours (ASTM B117)
IV. Industry trends and Seven PCBA InC solutions
4.1 Technology evolution direction
- 2025 forecast:
- 800V high-voltage fast charging will be popularized, and PCBA needs to support SiC full-bridge topology
- V2G (vehicle to grid) function becomes standard
- AIoT integration: Charging piles participate in smart cities as edge computing nodes
4.2 Core advantages of Seven PCBA InC
- Differentiated services:
- Customized design: Support OEM/ODM mode, and deliver prototypes in as fast as 7 days
- Global Certification: Provide CE, FCC, CB and other 15 certification agency services
- After-sales guarantee: 3-year warranty + 24-hour response
V. Summary and Action Guide
The intelligent upgrade of new energy charging piles has entered the PCBA deep customization era. Through high integration design, multimodal communication and AI algorithm empowerment, PCBA solutions are reshaping the efficiency boundaries of charging piles. For enterprises, choosing a PCBA supplier with vertical integration capabilities (such as Seven PCBA InC) can not only shorten the R&D cycle by 30%, but also reduce the cost of a single device by 15%-20% through scale manufacturing.