-
Xinxintian Industrial Zone, Shajing Street,Bao'an District, Shenzhen, China
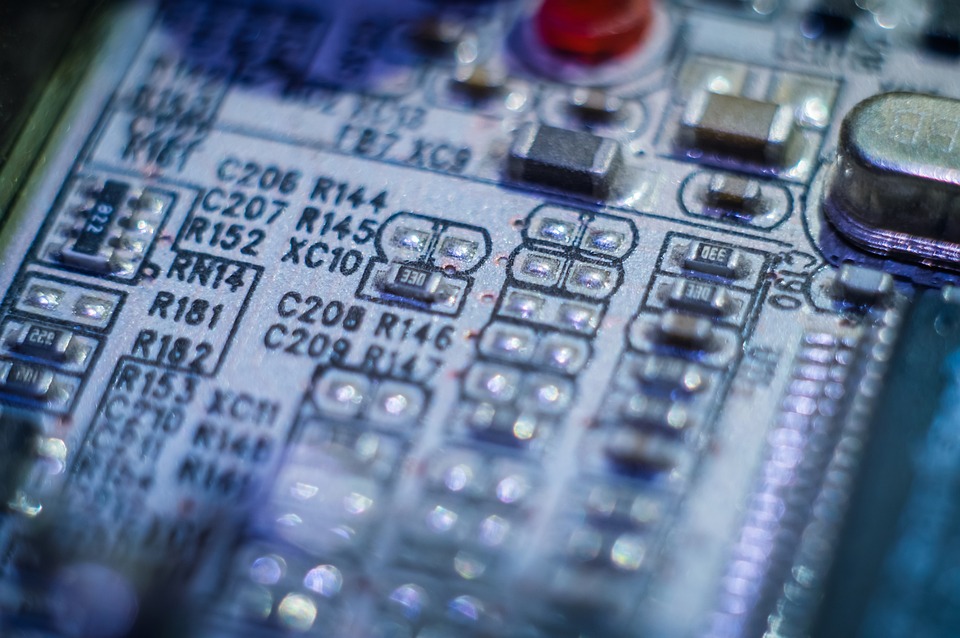
Top 5 Common Mistakes to Avoid When Choosing a PCB Assembly Service Provider
[ad_1]
Top 5 Common Mistakes to Avoid When Choosing a PCB Assembly Service Provider
When it comes to determining the right PCB assembly service provider for your next project, it can be overwhelming to navigate the vast array of options available. From finding the most cost-effective solution to ensuring the quality of the end product, it’s easy to get lost in the sea of choices. In this article, we’ll explore the top 5 common mistakes to avoid when choosing a PCB assembly service provider, helping you make an informed decision that meets your needs and exceeds your expectations.
1. Failing to Define Your Requirements
Before starting the search for a PCB assembly service provider, it’s crucial to define your requirements. What are your project’s specifications? What are your tolerances? What is your budget? What kind of certifications do you need? Failing to identify your needs will lead to a mismatch between what you want and what the service provider can deliver, resulting in delays, cost overruns, or even project cancellation. Make a list of your must-haves, nice-to-haves, and deal-breakers to ensure you’re choosing the right fit.
2. Focusing on Price Alone
It’s tempting to prioritize cost when selecting a PCB assembly service provider, but do so at your own peril. A low-cost option may save you money in the short term, but it may compromise on quality, lead time, and customer support, leading to long-term costs and headaches. Look instead for a balance between cost and value, considering factors like expertise, certifications, and track record. Remember, cheap can be expensive in the long run.
3. Neglecting Certifications and Compliance
Whether it’s ISO 9001, ISO 13485, or IPC-610, various certifications and compliance standards are essential for ensuring the quality and reliability of PCB assemblies. Check that the service provider you’re considering has the necessary certifications and complies with industry regulations. Failing to do so may mean a subpar product that doesn’t meet your requirements, which can affect the integrity of your project and your reputation.
4. Ignoring Industry Experience and Expertise
Industry experience and expertise are crucial in the world of PCB assembly, where precision and attention to detail are paramount. A service provider with years of experience working with similar projects and technologies is more likely to deliver high-quality results, minimize delays, and provide valuable insights during development. Look for a provider with a proven track record in your specific industry or technology, as well as a willingness to learn and adapt to your project’s unique needs.
5. Failing to Evaluate Communication and Support
Effective communication and support are vital for successful project outcomes. Look for a service provider that offers transparent, regular updates, and clear communication channels throughout the project. Check their support for FAQs, documentation, and training materials, as well as their responsiveness to concerns and issues. A provider that listens, adapts, and adapts to your needs is more likely to deliver a product that meets your expectations and your customers’ needs.
Conclusion
Choosing the right PCB assembly service provider is a crucial step in the development of your project, and it’s crucial to avoid common pitfalls that can jeopardize quality, timeliness, and budget. By defining your requirements, balancing cost and value, considering certifications and compliance, ignoring industry expertise, and evaluating communication and support, you’ll be well on your way to selecting a provider that meets your needs and exceeds your expectations. Remember, taking shortcuts or making assumptions can lead to costly mistakes, so take the time to research, discuss, and consider the importance of PCB assembly in your project’s success.
FAQs
Q: What are the most common reasons for PCB assembly project failure?
A: The most common reasons for project failure are unclear requirements, unrealistic timelines, and inadequate budgeting.
Q: What certifications should I look for in a PCB assembly service provider?
A: Look for certifications such as ISO 9001, ISO 13485, and IPC-610, which ensure quality and reliability in the manufacturing process.
Q: How do I ensure timely delivery of the final product?
A: Clear communication, regular updates, and a detailed project plan are essential for avoiding delays. Look for a service provider that provides a clear project timeline and updates regularly throughout the process.
Q: What are the benefits of partnering with a PCB assembly service provider?
A: Among the benefits are cost savings, reduced lead time, and increased efficiency, allowing you to focus on core competencies and improve overall project outcomes.
Q: What should I look for in a PCB assembly service provider’s documentation and support?
A: Look for clear, concise documentation, as well as extensive FAQs, tutorials, and training materials to ensure a smooth transition and adequate support for your project team.
[ad_2]