-
Xinxintian Industrial Zone, Shajing Street,Bao'an District, Shenzhen, China
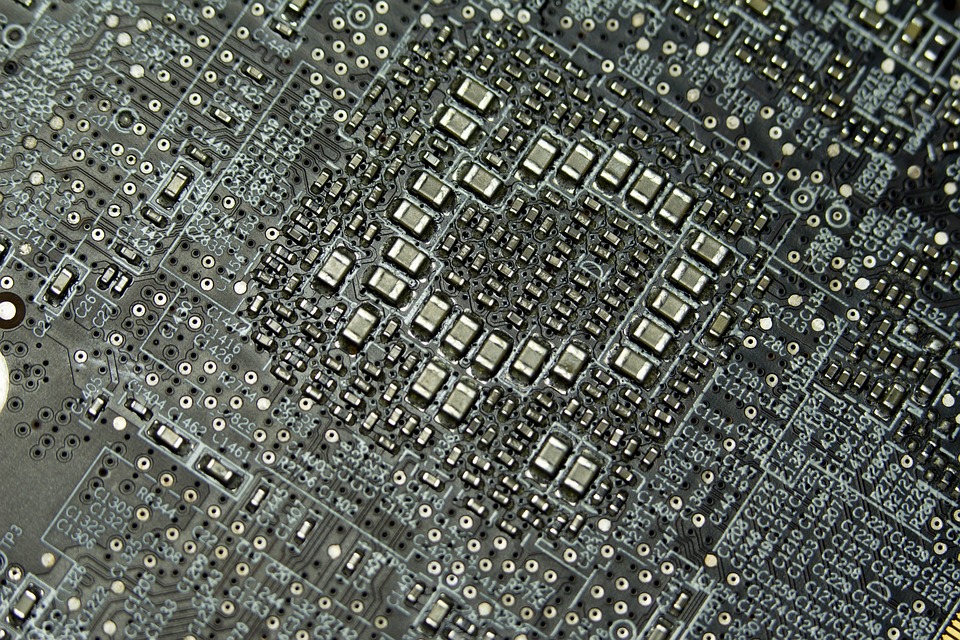
PCB Design for Manufacturability (DFM): A Comprehensive Guide
[ad_1]
PCB design for manufacturability (DFM) is a critical aspect of electronic design automation (EDA) that involves designing printed circuit boards (PCBs) with manufacturability in mind. In this article, we will explore the importance of PCB DFM, its benefits, and best practices to ensure successful implementation.
The Importance of PCB DFM
PCB DFM is crucial because it enables designers to produce high-quality, cost-effective, and reliable PCBs that meet the requirements of the manufacturing process. Poorly designed PCBs can lead to increased production costs, rework, and even product recalls. DFM ensures that designers consider the manufacturing process and its challenges while designing the PCB, resulting in a smoother, faster, and more efficient production process.
The benefits of PCB DFM include:
- Reduced design cycle time
- Lower production costs
- Improved product reliability
- Increased design yield
Challenges in PCB DFM
Designers face several challenges when designing for manufacturability, including:
- Limited design experience and knowledge of manufacturing processes
- Lack of collaboration between design and manufacturing teams
- Inadequate design for manufacturing tools and software
- Variability in manufacturing processes and materials
Best Practices for PCB DFM
To achieve successful PCB DFM, designers should follow these best practices:
- Conduct thorough design reviews and analysis
- Use design for manufacturability (DFM) software tools and plugins
- Collaborate with manufacturing teams early in the design process
- Consider manufacturing processes and materials during the design phase
- Use design rules checks (DRCs) and design rule files (DRFs)
- Optimize component placement and routing
- Use simplified design for manufacture (SDFM) techniques
DFM Software Tools
Several software tools are available to support PCB DFM, including:
- DFM software plugins for popular CAD software
- Design for manufacturability (DFM) checkers
- Manufacturability-aware design rules and constraints
- 3D and 2D design collaboration tools
DFM in Industry 4.0
The increasing adoption of Industry 4.0 technologies is driving the demand for PCB DFM. The integration of artificial intelligence (AI), machine learning (ML), and Internet of Things (IoT) into manufacturing is transforming the way PCBs are designed, produced, and used. DFM is critical in this context, as it ensures that PCBs are designed to work seamlessly with Industry 4.0 technologies and can withstand the increased complexity and variability of modern manufacturing lines.
Conclusion
In conclusion, PCB DFM is a critical aspect of electronic design automation that requires careful consideration of manufacturing processes and materials during the design phase. By following best practices, using DFM software tools, and understanding the challenges and benefits of DFM, designers can ensure that their PCBs are manufactured efficiently, effectively, and to the required quality standards.
FAQs
What is PCB DFM?
PCB DFM is the process of designing printed circuit boards (PCBs) with manufacturability in mind, ensuring that they can be produced efficiently and effectively.
Why is PCB DFM important?
PCB DFM is critical because it enables designers to produce high-quality, cost-effective, and reliable PCBs that meet the requirements of the manufacturing process, reducing the risk of rework, production delays, and product recalls.
What are the benefits of PCB DFM?
The benefits of PCB DFM include reduced design cycle time, lower production costs, improved product reliability, and increased design yield.
What are the challenges in PCB DFM?
The challenges in PCB DFM include limited design experience and knowledge of manufacturing processes, lack of collaboration between design and manufacturing teams, inadequate design for manufacturing tools and software, and variability in manufacturing processes and materials.
What are the best practices for PCB DFM?
The best practices for PCB DFM include conducting thorough design reviews and analysis, using design for manufacturability (DFM) software tools and plugins, collaborating with manufacturing teams early in the design process, and considering manufacturing processes and materials during the design phase.
What is Industry 4.0 in relation to PCB DFM?
The increasing adoption of Industry 4.0 technologies is driving the demand for PCB DFM, as it ensures that PCBs are designed to work seamlessly with Industry 4.0 technologies and can withstand the increased complexity and variability of modern manufacturing lines.
[ad_2]