-
Xinxintian Industrial Zone, Shajing Street,Bao'an District, Shenzhen, China
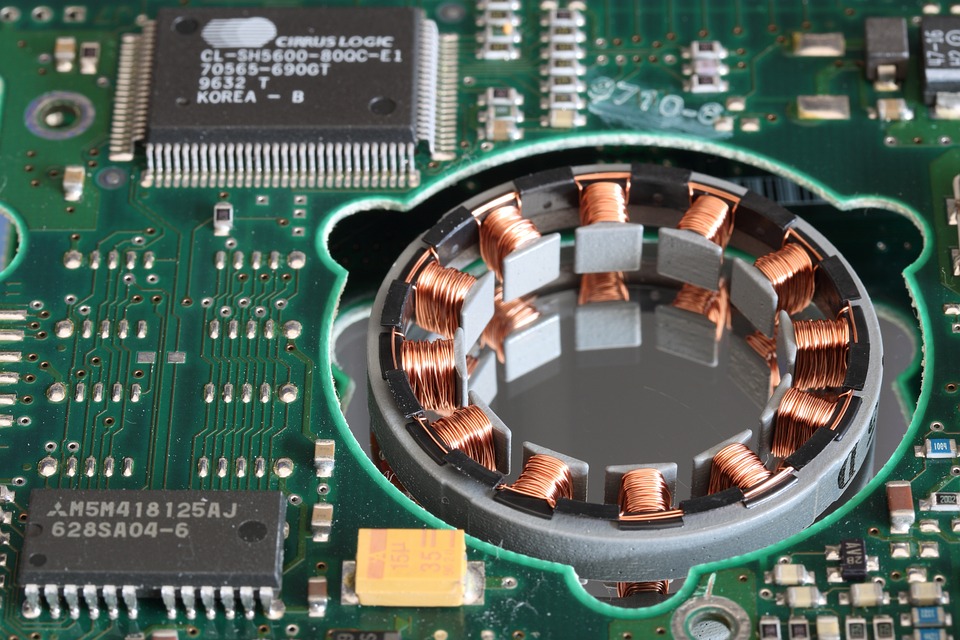
PCB Assembly Design for Manufacturing (DFM): A Guide to Making it Right the First Time
[ad_1]
Content Here
Purpose and Importance of PCB Assembly Design for Manufacturing (DFM)
The design for manufacturing (DFM) is a crucial step in the printed circuit board (PCB) assembly process. DFM ensures that the design of the PCB is optimal for manufacturing, taking into account the limitations and capabilities of the manufacturing process. This ensures that the PCB is manufactured correctly the first time, with reduced costs, errors, and production time.
The importance of DFM cannot be overstated. A well-designed PCB that is manufactured correctly is essential for the successful operation of today’s complex electronic devices. A PCB that is not well-designed can lead to communication errors, diminished performance, and even device failure.
Design Guidelines for DFM
Here are some key design guidelines for a PCB design for manufacturing:
- Layer Stack-up: A well-designed layer stack-up ensures that signal integrity is maintained, and the PCB is easy to manufacture. This involves the careful selection of material, thickness, and arrangement of layers to ensure optimal performance.
- Component Placement: Careful placement of components is crucial for ensuring the optimal flow of signals, heat dissipation, and efficient repair. This also ensures that components are easily accessible for replacement and maintenance.
- Routing: The routing of PCB traces should be efficient, with a minimum number of vias, to reduce manufacturing risks and ensure signal integrity. This also helps to reduce the risk of errors and rework.
- Component Spacing and Orientation: Adequate spacing and orientation of components are critical for ensuring the correct flow of signals, heat dissipation, and efficient repair. The component spacing should also ensure that adjacent components can be easily replaced.
- Boundary Scan and Contigous Paddle: Implementing a boundary scan and contiguous paddle ensures that the PCB is easily programmable and reduces the risk of software bugs. This also reduces the risk of board-level faults and improves diagnosis and debugging.
- PDM and Assembly Tooling: Using PDM (Product Data Management) and assembly tooling ensures efficient communication between design, manufacturing, and test teams. This ensures that the PCB design is tailored to the manufacturing process, reducing errors, and improving quality.
- Iterative Design and Verification: A well-structured design that includes iterative design and verification ensures that the PCB design is optimal for manufacturing. This involves repeated iterations of design and verification to identify and address potential issues early on.
- Electromagnetic Compatibility (EMC) and Thermal Analysis: Conducting EMC and thermal analysis early in the design cycle ensures that the PCB is optimized for both thermal and electromagnetic performance, reducing the risk of design flaws and costly rework.
- Documentation and Change Management: Clear documentation and change management ensures that all stakeholders, including manufacturing, testing, and maintenance, have access to accurate and up-to-date information. This improves communication, reduces errors, and minimizes downtime.
Best Practices for Successful DFM
To ensure a successful DFM process, follow these best practices:
- Involve manufacturing early and early:** Involve manufacturing early and often in the design process to ensure that the design is optimized for manufacturing. This ensures that the design takes into account the limitations and capabilities of manufacturing, resulting in a PCB that is manufactured correctly the first time.
- Use standardized design tools and language:** Use standardized design tools and language to ensure seamless communication between design, manufacturing, and test teams. This reduces errors, improves quality, and minimizes downtime.
- Implement design reviews and checks:** Implement regular design reviews and checks to ensure that the design meets manufacturing requirements. This includes undergoing design for manufacturing (DFM) checks, electrical checks, and thermal checks.
- Use PDM and assembly tooling:** Use PDM and assembly tooling to ensure efficient communication between design, manufacturing, and test teams. This reduces errors, improves quality, and minimizes downtime.
- Conduct a design for testability (DFT) analysis:** Conduct a DFT analysis to identify potential issues and ensure that the PCB is testable. This includes identifying and addressing issues with test access, coverage, and testability.
- Implement a version control system:** Implement a version control system to track changes and maintain a record of design modifications. This ensures that changes are documented and easily accessible, reducing errors and improving quality.
- Conduct a systematic design review:** Conduct a systematic design review to identify and address potential issues early on. This includes reviewing the design against DFM guidelines, electrical, and thermal requirements.
Why DFM is Important in PCB Design
DFM is crucial for the production of high-quality, reliable, and cost-effective PCBs. With its importance, companies cannot afford to compromise on design for manufacturing. The following reasons highlight the importance of DFM in PCB design:
- with reduced waste and scrap:** By designing with manufacturing in mind, companies can reduce waste and scrap, leading to cost savings and improved efficiency.
- reduces the risk of design flaws and manufacturing errors:** A well-designed PCB reduces the risk of design flaws and manufacturing errors, leading to improved quality, reliability, and reduced downtime.
- services and cost savings:** DFM enables companies to reduce costs, improve quality, and enhance efficiency, leading to improved performance, competitiveness, and customer satisfaction.
- 4371 Problem-Reactive Thinking:** By adopting a reactive, problem-based approach to PCB design, companies can reduce the risk of design flaws, improve quality, and enhance customer satisfaction, leading to improved performance, competitiveness, and profitability.
Conclusion
In conclusion, PCB design for manufacturing (DFM) is a crucial aspect of the PCB design process. By following best practices, guidelines, and incorporating DFM into the design process, companies can ensure that their PCBs are manufactured correctly the first time, with reduced costs, errors, and production time. This leads to improved quality, reliability, and customer satisfaction, and ultimately, better bottom-line performance.
Frequently Asked Questions
What is PCB Design for Manufacturing (DFM)?
PCB design for manufacturing (DFM) refers to the process of designing a PCB with manufacturing in mind, ensuring that the design is optimal for manufacturing and takes into account the limitations and capabilities of the manufacturing process.
What are the key guidelines for PCB design for manufacturing (DFM)?
Some key guidelines for PCB design for manufacturing (DFM) include layer stack-up, component placement, routing, component spacing and orientation, boundary scan and contiguous paddle, PDM and assembly tooling, iterative design and verification, electromagnetic compatibility (EMC) and thermal analysis, and documentation and change management.
What are some best practices for successful PCB design for manufacturing (DFM)?
Some best practices for successful PCB design for manufacturing (DFM) include involving manufacturing early and often, using standardized design tools and language, implementing design reviews and checks, using PDM and assembly tooling, conducting a design for testability (DFT) analysis, implementing a version control system, and conducting a systematic design review.
[ad_2]