-
Xinxintian Industrial Zone, Shajing Street,Bao'an District, Shenzhen, China
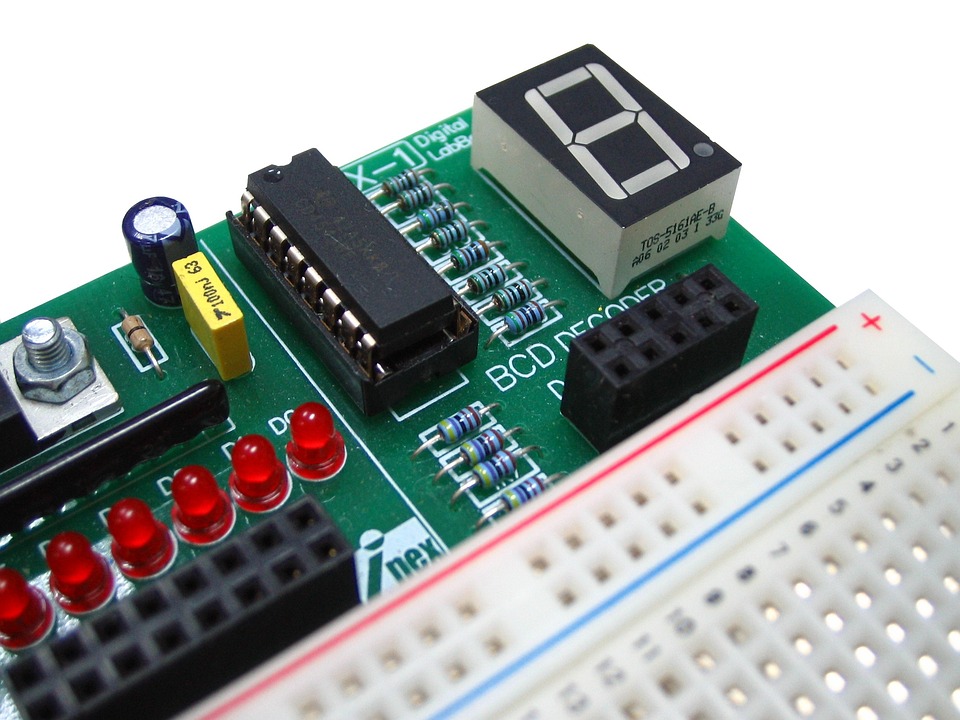
PCB Assembly Best Practices: Ensuring High-Quality Results and Efficient Production
[ad_1]
PCB Assembly Best Practices: Ensuring High-Quality Results and Efficient Production
PCB (Printed Circuit Board) assembly is a critical step in the production of electronic devices, requiring precision, attention to detail, and adherence to best practices to ensure high-quality results and efficient production. In this article, we will explore the best practices for PCB assembly, highlighting the key factors that contribute to successful outcomes and minimizing the risk of defects and rework.
Component Selection and Sourcing
The quality of components used in PCB assembly can significantly impact the overall performance and reliability of the final product. It is essential to select high-quality components from reputable suppliers, ensuring that they meet the required specifications and standards. When sourcing components, consider the following factors:
- Component specifications: Verify that the components meet the required specifications, including dimensions, materials, and performance characteristics.
- Supplier reputation: Research the supplier’s reputation, including their quality control processes, delivery times, and customer service.
- Component availability: Ensure that the components are readily available and can be delivered on time to meet production schedules.
- Cost and pricing: Balance the cost of components with the required quality and performance, ensuring that the final product meets budget constraints.
PCB Design and Layout
A well-designed PCB layout is critical to ensuring efficient assembly and minimizing the risk of defects. Consider the following best practices when designing and laying out PCBs:
- Component placement: Place components in a logical and organized manner, minimizing the risk of damage or interference during assembly.
- Routing and wiring: Use efficient routing and wiring techniques to minimize signal integrity issues and reduce the risk of defects.
- Component density: Balance component density with the need for easy assembly and maintenance, ensuring that components are not too close together or too far apart.
- PCB material selection: Select the appropriate PCB material based on the application, considering factors such as thermal conductivity, insulation, and durability.
Assembly Process and Techniques
The assembly process and techniques used can significantly impact the quality and efficiency of PCB assembly. Consider the following best practices:
- Surface mount technology (SMT): Use SMT for components that require precise placement and minimal soldering, such as capacitors, resistors, and ICs.
- Through-hole technology (THT): Use THT for components that require mechanical fastening, such as connectors, switches, and potentiometers.
- Soldering and reflow: Use controlled soldering and reflow techniques to ensure proper joint formation and minimize the risk of defects.
- Component orientation: Ensure that components are properly oriented during assembly to minimize the risk of damage or misalignment.
Quality Control and Inspection
Quality control and inspection are critical steps in the PCB assembly process, ensuring that the final product meets the required specifications and standards. Consider the following best practices:
- Visual inspection: Conduct regular visual inspections during assembly to detect defects and errors early on.
- X-ray inspection: Use X-ray inspection to detect internal defects, such as shorts or opens, that may not be visible during visual inspection.
- Functional testing: Conduct functional testing to ensure that the PCB meets the required specifications and standards.
- Documentation and records: Maintain accurate documentation and records of the assembly process, including component usage, assembly techniques, and quality control measures.
Conclusion
PCB assembly is a critical step in the production of electronic devices, requiring precision, attention to detail, and adherence to best practices to ensure high-quality results and efficient production. By selecting high-quality components, designing and laying out PCBs with care, using efficient assembly techniques, and implementing quality control and inspection measures, manufacturers can minimize the risk of defects and rework, ensuring the production of high-quality products that meet customer requirements and expectations.
FAQs
Q: What are the most common defects in PCB assembly?
A: The most common defects in PCB assembly include component misplacement, soldering defects, and electrical shorts or opens.
Q: How can I ensure that my PCB design is suitable for assembly?
A: Ensure that your PCB design is suitable for assembly by considering factors such as component placement, routing and wiring, and component density, and by using design tools and software to simulate and optimize the assembly process.
Q: What are the benefits of using surface mount technology (SMT) in PCB assembly?
A: The benefits of using SMT in PCB assembly include increased component density, reduced assembly time, and improved reliability and durability.
Q: How can I improve the quality of my PCB assembly process?
A: Improve the quality of your PCB assembly process by implementing quality control and inspection measures, such as visual inspection, X-ray inspection, and functional testing, and by training assembly personnel to follow best practices and procedures.
Q: What are the most common causes of PCB assembly defects?
A: The most common causes of PCB assembly defects include component defects, improper assembly techniques, and inadequate quality control and inspection measures.
Q: How can I reduce the risk of defects and rework in PCB assembly?
A: Reduce the risk of defects and rework in PCB assembly by selecting high-quality components, designing and laying out PCBs with care, using efficient assembly techniques, and implementing quality control and inspection measures.
Q: What are the benefits of using a PCB assembly service provider?
A: The benefits of using a PCB assembly service provider include access to specialized equipment and expertise, reduced capital expenditures, and improved quality and reliability of the final product.
Q: How can I ensure that my PCB assembly process is compliant with industry standards and regulations?
A: Ensure that your PCB assembly process is compliant with industry standards and regulations by implementing quality control and inspection measures, such as ISO 9001 and IPC-A-610, and by training assembly personnel to follow best practices and procedures.
[ad_2]