-
Industriegebiet Xinxintian, Shajing-Straße, Bezirk Bao'an, Shenzhen, China
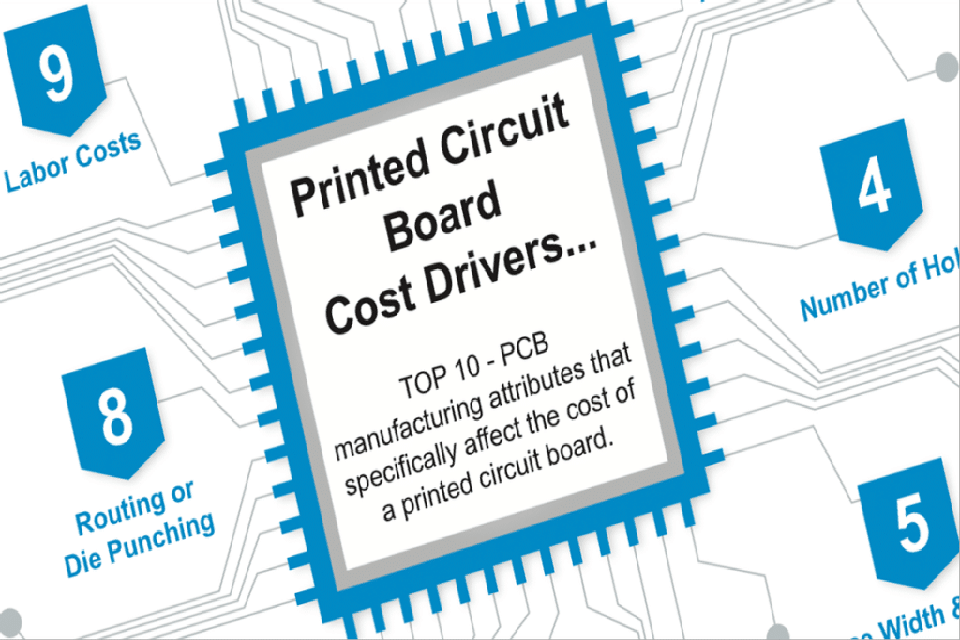
10 Tipps zur Reduzierung der PCB-Produktionskosten
Abstrakt
When many PCB purchasers or engineers look for PCB manufacturers to make boards, they always feel that the pcb production cost is high, but they don’t know where and why the cost is too high, and they don’t know how to optimize the cost while ensuring the quality of the circuit board. They can only compare prices from three suppliers and give it to whoever has the lowest price. But in fact, this method is wrong. This cannot choose the most suitable and cost-effective supplier. Today, the editor shares a super practical PCB purchasing guide-10 tips to reduce PCB costs! It is strongly recommended to collect!
Inhaltsverzeichnis
1. verschiedene Markenmaterialien
For example, for boards with TG value ≥150°, multi-layer boards, and PP sheet dielectric thickness exceeding 0.2mm, Guoji will be cheaper than KB, Shengyi, and Nanya, but Guoji is generally used for single-sided and double-sided boards, and it is not recommended to use them for multi-layer boards. There are also some unknown brands of boards, which are cheaper and can be used, but the performance is relatively poor, and the probability of quality problems will be higher. If you make a PCB with more than 8 layers, you need to choose a board with better performance. It is recommended to use KB TG170, which is more cost-effective.
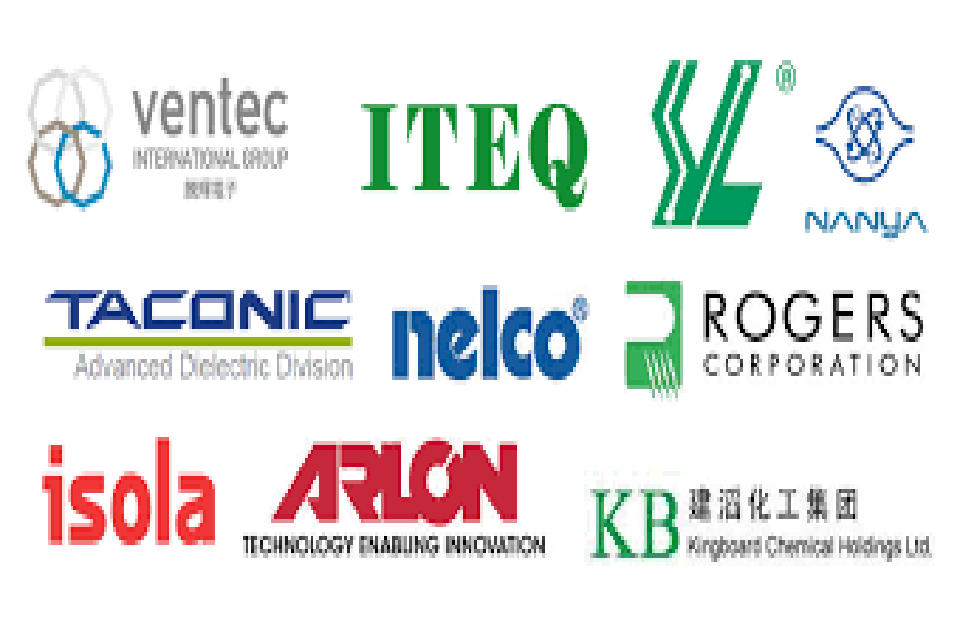
2. Lötstopplack
solder mask two points: color and brand.
In terms of color, the most common is green ink, but if you want to use special color ink, such as blue oil, white oil, butter oil, black oil, etc., there will generally be a price increase. In terms of brand, the best one at present is Sun ink, which is mainly characterized by high viscosity, stable dielectric constant, good insulation and anti-oxidation, but it is relatively expensive. Other brands of ink are relatively cheaper, but the quality is not particularly stable. If it is used in batches, I personally recommend using Sun ink, which has stable quality and relatively stable product operation.
3. PCB-Folie
If the film is a simple material,for batch boards with a line width and spacing of more than 5/5mil, manufacturers will choose to use film in order to achieve production capacity. The larger the size of the board, the higher the film cost, and the general minimum cost is between 100-200. (Small batch sample production usually uses LDI exposure machine, not film; and batch production will use film first and then LED traditional exposure in order to pursue production capacity.)
4. Trace line width and spacing
the higher the price. If the line width and line spacing are less than 5/5mil, there will generally be a price increase. Because the thinner the wire, the higher the precision of the equipment and the quality of the chemical solution are required, and the yield rate will be relatively low, resulting in higher costs. However, the thinner the wire, the higher the price is not absolute. For example, some board manufacturers may hold activities and do not charge extra fees for thin wires.
5. Drill size
the higher the price. The diameter below 0.3mm will be increased; the more holes, the higher the price. Other special holes will also increase the cost, such as half holes, PTH holes larger than 6.0mm, etc. Because the holes are small, only one board can be drilled at a time when drilling holes in PCB materials, which is inefficient and the possibility of drill bit breaking is also greater, resulting in higher costs.
6. Finish Copper thickness
The cost of boards with copper thickness≥2oz and hole copper greater than 25μm will increase. Because the price of copper itself is relatively expensive, the thicker the copper, the higher the price. In addition, the cost of additional electrolytic copper leads to an overall price increase.
7. PCB finish board thickness
The price of PCBs with a thickness of 1.2 or 1.6 mm is not much different, but if the thickness is 2.0 mm or even thicker, the cost will increase accordingly. The thicker the board, the more sheets of fiberglass cloth, so the cost will increase accordingly.
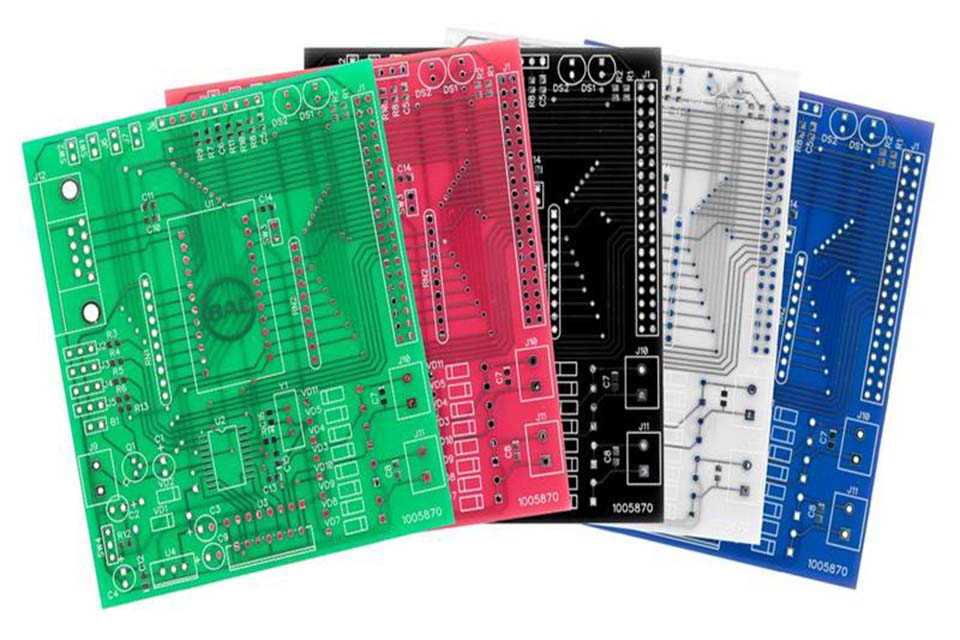
8.PCB shape
If the appearance data has more grooves and the grooves are less than 1.0 mm in size, the cost will increase. This is because the boards with more grooves are mostly irregular, which leads to the processing time being extended. In addition, if the width of the groove is small, the processing cannot be too fast, and the milling cutter is easy to break, so the processing efficiency is low, and the production cost naturally increases.
9. Surface finish
Our common surface treatment processes include: OSP (anti-oxidation), lead tin spraying, lead-free tin spraying (environmental protection), gold plating, immersion gold and some combined processes. The price of the above processes is more expensive, that is: OSP (anti-oxidation) < lead tin spraying < lead-free tin spraying (environmental protection) < gold plating < immersion gold.
It is worth mentioning that most of them do lead/lead-free tin spraying because of their high cost performance. But some manufacturers’ OSP process is even more expensive than tin spraying! This is because for cost considerations, the sample factory will put together the boards of the same process for multiple customers for shipment, but because OSP is difficult to tin, fewer customers need it, which makes it difficult to assemble the boards of OSP process, and they can only be shipped separately, so the price will increase by dozens of yuan.
10. Mold fee and test fee Mold fee:
If it is for proofing or small batches, the general board factory uses drilling and milling, and no additional milling fee is required. But if it is a large batch, it is necessary to open a mold to punch the board, which will generate a set of mold fees. The board factory generally quotes more than 1,000 143USD. Test fee: If it is a proofing or small batch, flying probe testing is generally used, and the cost ranges from 100 to 400 yuan (depending on the number of test points in the file).
If it is a large batch, a test frame must be opened for testing, which is efficient and has a lower overall cost! The cost of the test frame is generally between 1,000 and 1,500 yuan. Summary: In summary, it is not necessary for the product itself. Before manufacturing the board, you must fully consider the cost. The above 10 aspects must be considered in place.
Zusammenfassung
SevenPCBA has more than 13 years of production experience and advanced production technology, equipment, etc., and has flexible and powerful capabilities to help you find the most suitable production and processing solution. If you have any PCB production needs, you can contact them for a free price evaluation.