-
Xinxintian Industrial Zone, Shajing Street,Bao'an District, Shenzhen, China
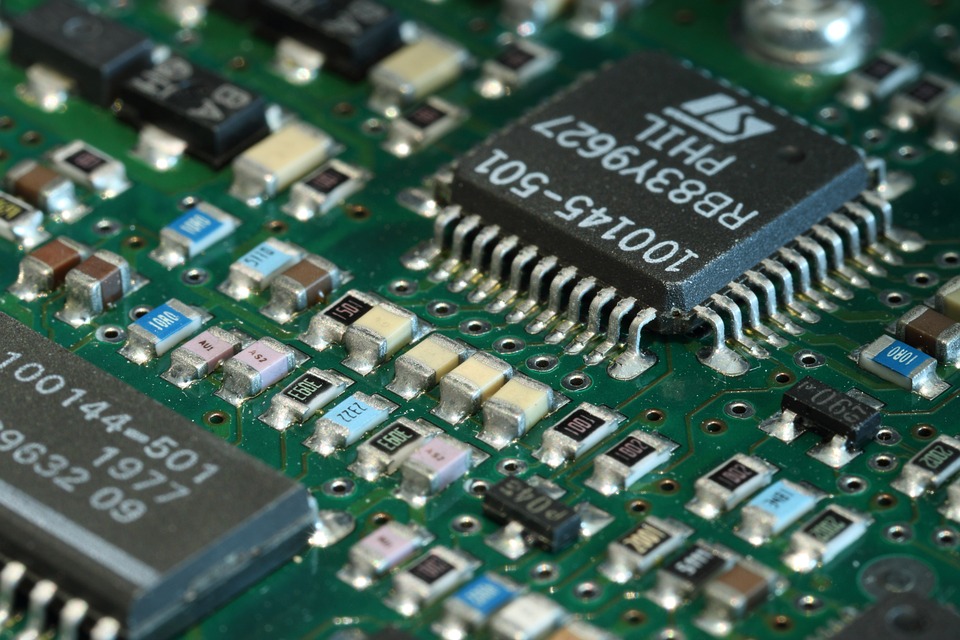
The Importance of Quality Control in PCB Assembly Services: What You Need to Know
[ad_1]
The importance of quality control in PCB assembly services cannot be overstated. With the rise of the internet of things (IoT) and the increasing complexity of electronic devices, the demand for high-quality printed circuit boards (PCBs) has never been higher. PCBs are the backbone of modern electronics, and any defects or flaws in their design or manufacturing can have serious consequences for the overall performance and reliability of the finished product.
PCB assembly services involve a range of complex processes, from design and fabrication to assembly and testing. At each stage, there is an opportunity for errors or defects to occur, which can compromise the quality of the final product. This is where quality control comes in – a critical process that ensures the PCB meets the required standards and specifications.
So, what do you need to know about quality control in PCB assembly services? Let’s start with the basics.
The Importance of Quality Control
Quality control is a systematic process that is designed to ensure that the PCB meets the required standards and specifications. It involves a range of activities, including inspection, testing, and documentation. The primary goal of quality control is to identify and eliminate defects or flaws in the PCB, thereby ensuring that the finished product is reliable, efficient, and meets the customer’s expectations.
Quality control is important for several reasons:
Ensures compliance with industry standards and regulations
Reduces the risk of product failure or defects
Improves product performance and reliability
Enhances customer satisfaction and loyalty
Reduces waste and minimizes the risk of rework or re-manufacturing
Quality Control Procedures
Quality control procedures typically involve a range of activities, including:
Inspection: Visual inspection of the PCB to identify any defects or flaws
Testing: Functional testing of the PCB to ensure it meets the required specifications
Documentation: Accurate and complete documentation of the PCB’s design, manufacturing, and testing
Failure Mode and Effects Analysis (FMEA): Identification and analysis of potential failure modes and their effects on the PCB’s performance
Continuous Improvement: Regular review and improvement of quality control procedures to ensure they are effective and efficient
These procedures are typically carried out at each stage of the PCB assembly process, from design and fabrication to assembly and testing. The specific procedures used may vary depending on the type of PCB, the customer’s requirements, and the manufacturer’s capabilities.
Benefits of Quality Control
The benefits of quality control in PCB assembly services are numerous and significant. Some of the most important benefits include:
Improved product reliability and performance
Reduced warranty claims and product returns
Enhanced customer satisfaction and loyalty
Reduced costs and improved efficiency
Compliance with industry standards and regulations
Conclusion
In conclusion, quality control is a critical process in PCB assembly services that ensures the finished product meets the required standards and specifications. It involves a range of activities, including inspection, testing, and documentation, and is essential for ensuring product reliability, performance, and customer satisfaction. By understanding the importance and procedures of quality control, customers can ensure they receive high-quality PCBs that meet their specific requirements.
FAQs
Q: What is quality control in PCB assembly services?
A: Quality control is a systematic process that is designed to ensure that the PCB meets the required standards and specifications.
Q: Why is quality control important in PCB assembly services?
A: Quality control is important to ensure compliance with industry standards and regulations, reduce the risk of product failure or defects, improve product performance and reliability, enhance customer satisfaction and loyalty, and reduce waste and minimize the risk of rework or re-manufacturing.
Q: What are the benefits of quality control in PCB assembly services?
A: The benefits of quality control in PCB assembly services include improved product reliability and performance, reduced warranty claims and product returns, enhanced customer satisfaction and loyalty, reduced costs and improved efficiency, and compliance with industry standards and regulations.
Q: How is quality control carried out in PCB assembly services?
A: Quality control is carried out through a range of activities, including inspection, testing, and documentation. The specific procedures used may vary depending on the type of PCB, the customer’s requirements, and the manufacturer’s capabilities.
Q: Why is continuous improvement important in quality control?
A: Continuous improvement is important in quality control because it ensures that the process is regularly reviewed and improved to ensure it is effective and efficient. This helps to identify and eliminate defects or flaws in the PCB, thereby ensuring that the finished product meets the required standards and specifications.
[ad_2]