-
Zona industriale di Xinxintian, Shajing Street, distretto di Bao'an, Shenzhen, Cina
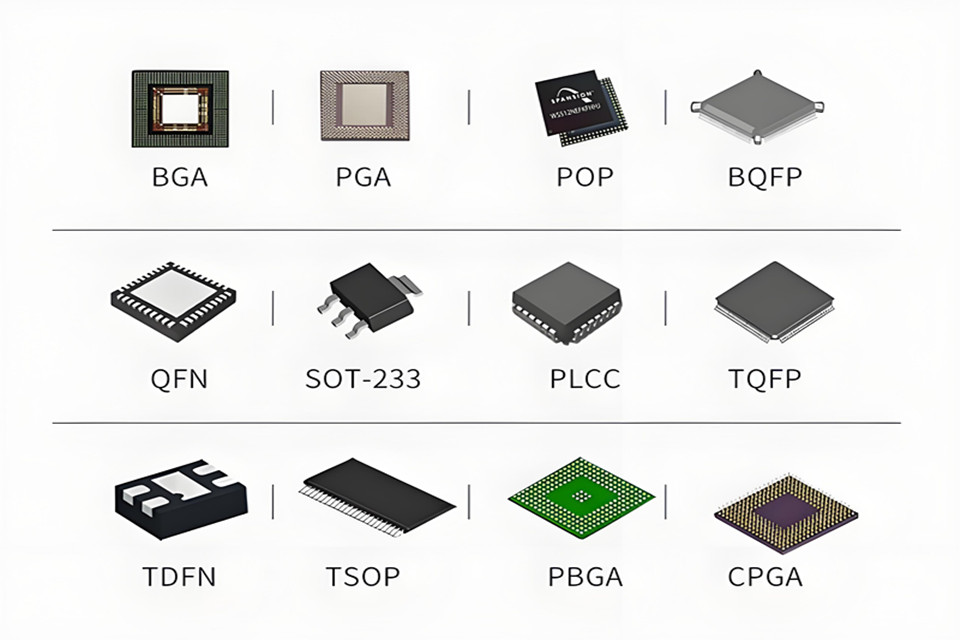
BGA contro QFP contro QFP
Con il rapido sviluppo della tecnologia elettronica, la tecnologia di confezionamento dei chip, in quanto collegamento fondamentale tra dispositivi semiconduttori e circuiti stampati, influisce direttamente sulle prestazioni, sull'affidabilità e sui costi delle apparecchiature. BGA (Ball Grid Array), QFP (pacchetto quadruplo piatto) E LGA (Land Grid Array) sono tre forme di imballaggio principali, che soddisfano diverse esigenze applicative attraverso diverse strutture fisiche e caratteristiche di processo.
- Confezionamento BGA È noto per il suo array di sfere di saldatura ad alta densità. Grazie alle sue eccellenti prestazioni ad alta frequenza e alla sua elevata capacità di dissipazione del calore, è diventato la scelta ideale per il calcolo ad alte prestazioni, le comunicazioni 5G e i dispositivi mobili;
- Imballaggio QFP si basa su un design a pin a quattro lati ed è ampiamente utilizzato nell'elettronica di consumo e in scenari generali grazie ai suoi bassi costi e ai vantaggi di facile rilevamento;
- Imballaggio LGA consente di ottenere una maggiore affidabilità tramite una matrice di contatti collegabili, in particolare nel campo delle CPU desktop e del controllo industriale.
Sommario
In questo articolo verranno analizzati in modo approfondito i principi, i vantaggi, gli svantaggi e gli scenari applicativi tipici di queste tre tecnologie di packaging, per aiutare ingegneri e sviluppatori a effettuare la scelta migliore in base alle esigenze reali.
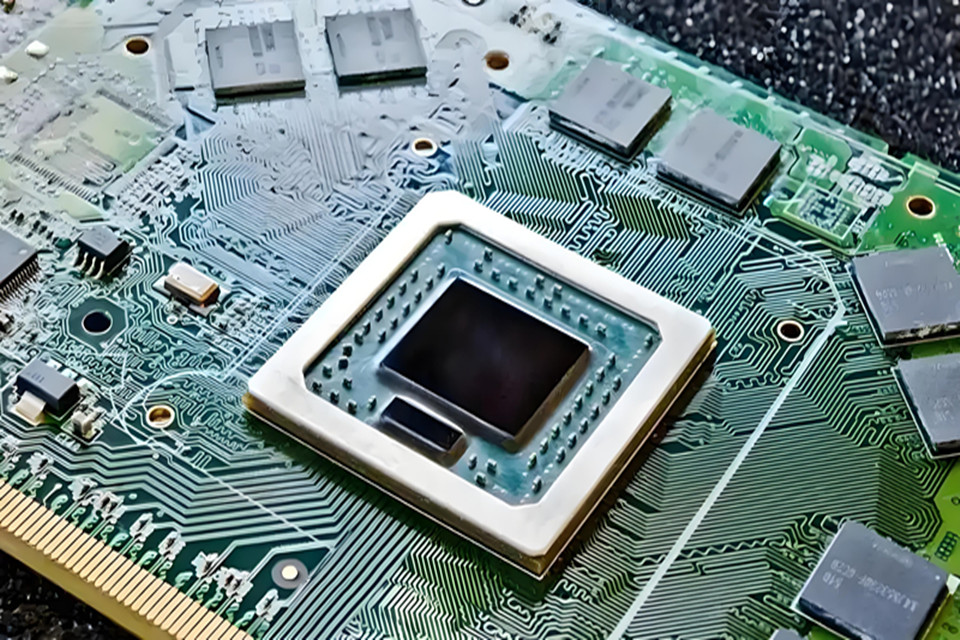
Abstract dell'articolo
- Pacchetto BGA
- Caratteristiche: Adotta una matrice di sfere di saldatura inferiori per fornire alta densità I/O (il numero di pin può raggiungere centinaia o addirittura migliaia), piccolo ritardo nella trasmissione del segnale, elevata efficienza di dissipazione del calore e volume ridotto di oltre 50% rispetto ai pacchetti tradizionali.
- Vantaggi: Eccellenti prestazioni ad alta frequenza, elevata stabilità meccanica, adatto a scenari di elevata integrazione (come chip per server, processori per smartphone).
- Svantaggi:Non può essere sostituito dopo la saldatura, richiede un'ispezione a raggi X e presenta elevati costi di rilavorazione.
- Pacchetto QFP
- Caratteristiche: Disposizione dei pin a quattro lati, processo maturo, basso costo, adatto per applicazioni a media e bassa densità.
- Vantaggi: Rilevamento intuitivo, supporta il montaggio superficiale SMT, adatto per campi elettronici generali quali sensori e dispositivi a bassa potenza.
- Svantaggi:Una spaziatura ridotta tra i pin comporta elevati parametri parassiti, scarsa capacità di dissipazione del calore e prestazioni ad alta frequenza limitate.
- Pacchetto LGA
- Caratteristiche:Si collega al socket della scheda madre tramite il contatto inferiore, supporta il design plug-in e ha un'elevata affidabilità.
- Vantaggi: elevate capacità di gestione termica, facile installazione, buona stabilità a lungo termine, ampiamente utilizzato nelle CPU desktop (come la serie Intel LGA) e nei sistemi di controllo industriale.
- Svantaggi: grandi dimensioni, richiede prese aggiuntive e costo elevato.
Riepilogo:
- BGA è adatto a scenari con rigorosi requisiti di prestazioni (come elaborazione ad alte prestazioni, moduli di comunicazione);
- QFP è la prima scelta per applicazioni generiche e a basso costo (come l'elettronica di consumo);
- LGA offre buone prestazioni in aree che richiedono aggiornabilità e stabilità (ad esempio, i processori desktop).
Confrontando le prestazioni elettriche, la gestione termica, i costi e la manutenibilità dei tre, gli ingegneri possono scegliere in modo flessibile le soluzioni di imballaggio in base ai requisiti del prodotto per bilanciare prestazioni, costi e affidabilità.
Di seguito è riportata una tabella di confronto delle prestazioni tra Pacchetto BGA E Pacchetto QFP
Confronto delle prestazioni BGA vs QFP
Dimensioni di confronto | Pacchetto BGA | Pacchetto QFP |
---|---|---|
Densità I/O | Alta densità I/O, layout array a sfere di saldatura, il numero di pin supera di gran lunga QFP | Numero medio di pin, disposizione a quattro lati, adatta per applicazioni a media e bassa densità |
Prestazioni elettriche | Piccolo ritardo nella trasmissione del segnale, percorso breve della sfera di saldatura, basso rumore, eccellenti prestazioni ad alta frequenza | Parametri parassiti elevati, pin lunghi, prestazioni ad alta frequenza limitate |
Gestione termica | Elevata efficienza di dissipazione del calore, ampia area di contatto della sfera di saldatura, eccellente conduttività termica | Capacità generale di dissipazione del calore, dipendente dai pin e dai materiali di imballaggio, elevata resistenza termica |
Affidabilità | Saldatura complanare, connessione stabile della sfera di saldatura, forte resistenza alle sollecitazioni meccaniche | Gli spilli si rompono facilmente, sensibile alle sollecitazioni meccaniche, bassa affidabilità a lungo termine |
Dimensioni e peso | Piccole dimensioni, lo spessore è 50% inferiore a QFP, risparmiando spazio sul PCB | Ampia area, pin esposti, adatti per applicazioni con spazio libero |
Costo di produzione | Elevati costi di produzione, attrezzature e processi ad alta precisione richiesti | Basso costo, processo semplice, adatto a prodotti di fascia media e bassa |
Rilevamento e riparazione | Rilevamento difficile, Rilevamento a raggi X richiesto, attrezzatura professionale richiesta per la rielaborazione | Rilevamento intuitivo, la qualità della saldatura può essere controllata a occhio nudo, la rilavorazione è relativamente semplice |
Scenari applicativi | Scenari ad alte prestazioni: CPU, GPU, chip per server, moduli di comunicazione 5G | Scenari generali: sensori, elettronica di consumo, dispositivi a basso consumo |
Complessità del processo | Produzione automatizzata, adatto per la produzione su larga scala | La saldatura manuale è fattibile, adatto per piccoli lotti o sviluppo di prototipi |
Corrispondenza di dilatazione termica | Ottimizzazione dell'adattamento termico, riducendo il rischio di affaticamento dei giunti di saldatura | Grande differenza di dilatazione termica, è facile che il pacco si guasti a causa della differenza di temperatura |
Di seguito è riportata una tabella di confronto delle prestazioni di Pacchetto BGA E Pacchetto LGA,
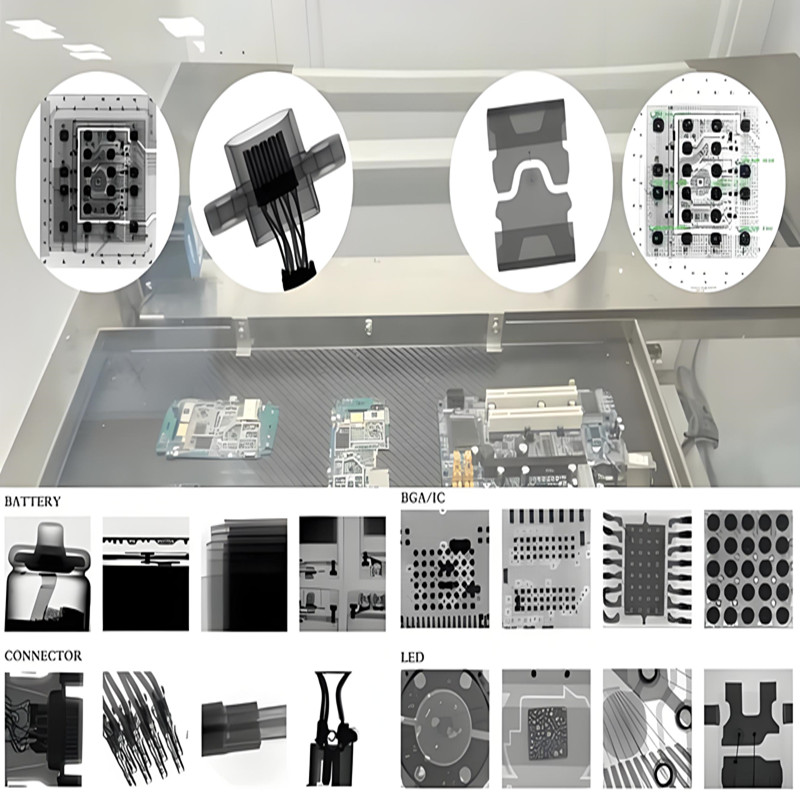
Confronto delle prestazioni BGA vs LGA
Dimensione di confronto | Pacchetto BGA | Pacchetto LGA |
---|---|---|
Metodo di connessione | matrice di sfere, saldato al PCB tramite sfere di saldatura inferiori | matrice di pad, contattando direttamente i pin della scheda madre tramite i pad metallici inferiori |
Sostituibilità | Non sostituibile, difficile da smontare dopo la saldatura (richiede un'operazione distruttiva) | Sostituibile, supporta il design plug-in (necessita di socket) |
Prestazioni di dissipazione del calore | Elevata efficienza di dissipazione del calore, le sfere di saldatura sono a diretto contatto con il PCB, breve percorso di conduzione del calore | Buone prestazioni di dissipazione del calore, dipende dall'area di contatto tra i pin e i pad della scheda madre |
Prestazioni elettriche | Piccolo ritardo nella trasmissione del segnale, percorso breve della sfera di saldatura, eccellenti prestazioni ad alta frequenza | Parametri parassiti bassi, elevata stabilità del segnale, adatto per applicazioni ad alta frequenza |
Volume e densità | Volume minimo, adatto per l'integrazione ad alta densità (come dispositivi mobili, chip server) | Volume leggermente più grande, i pin occupano più spazio |
Costo di produzione | Basso costo, processo di saldatura automatizzato maturo, adatto alla produzione su larga scala | Costo elevato, sono necessarie attrezzature di saldatura e prese ad alta precisione |
Processo di saldatura | Saldatura complanare, sono necessarie attrezzature ad alta precisione, la qualità della saldatura è controllata dalla temperatura | Saldatura a spina, la connessione avviene tramite prese e il processo di saldatura è più stabile |
Affidabilità | Alta affidabilità, connessione stabile della sfera di saldatura, forte resistenza alle sollecitazioni meccaniche | Alta affidabilità, ampia area di contatto tra perni e pad, buona stabilità a lungo termine |
Tasso di finitura | Basso tasso di finitura, la deviazione della saldatura porta facilmente alla rottura | Alto tasso di finitura, qualità di saldatura più controllabile |
Scenari applicativi | Scenari ad alte prestazioni: CPU, GPU, modulo di comunicazione 5G, chip del server | Scenari aggiornabili: CPU desktop, controllo industriale, apparecchiature elettroniche che necessitano di essere sostituite frequentemente |
Corrispondenza di dilatazione termica | Ottimizzazione dell'adattamento termico, ridurre il rischio di affaticamento dei giunti di saldatura | Grande differenza di dilatazione termica, è richiesto un ulteriore compenso materiale |
Rilevamento e riparazione | Rilevamento difficile, è richiesto il rilevamento a raggi X e sono necessarie attrezzature professionali per la rielaborazione | L'ispezione è intuitiva, la qualità della saldatura può essere controllata visivamente e la rilavorazione è relativamente semplice |
Aree di applicazione tipiche
- Confezionamento BGA: –dispositivi mobili: Smartphone, CPU/GPU per laptop
- Server: Chip di elaborazione ad alte prestazioni, controller di archiviazione
- Comunicazioni 5G: Moduli RF ad alta frequenza, chip per stazioni base
- Imballaggio LGA:
- PC desktop: CPU aggiornabile (come Intel LGA 1700)
- Controllo industriale: Sistemi embedded che necessitano di essere sostituiti frequentemente
- Mercato del fai da te: Progettazione della scheda madre che supporta la sostituzione da parte dell'utente
Riepilogo del confronto dei packaging BGA, QFP, LGA
Confezionamento BGA (Array di griglie di sfere) utilizza matrice di sfere di saldatura per raggiungere alta densità I/O E prestazioni ad alta frequenza, che è adatto per scenari ad alte prestazioni (come CPU, GPU, moduli di comunicazione 5G), ma presenta gli svantaggi di non sostituibile E difficile da rilevare; Imballaggio QFP (Pacchetto Quad Flat) adotta un spillo a quattro lati design, che è a basso costo e intuitivo da rilevare, ma ha parametri parassiti elevati E gestione termica debole, ed è adatto per elettronica di consumo generale (come sensori e dispositivi a basso consumo); Pacchetto LGA (Griglia terrestre) contatta i pin della scheda madre tramite un matrice di pad, supporta sostituibilità E alta affidabilità, ed è comunemente usato in CPU desktop E controllo industriale, ma è di grandi dimensioni E ad alto costo.