-
Zona industrial de Xinxintian, calle Shajing, distrito de Bao'an, Shenzhen, China
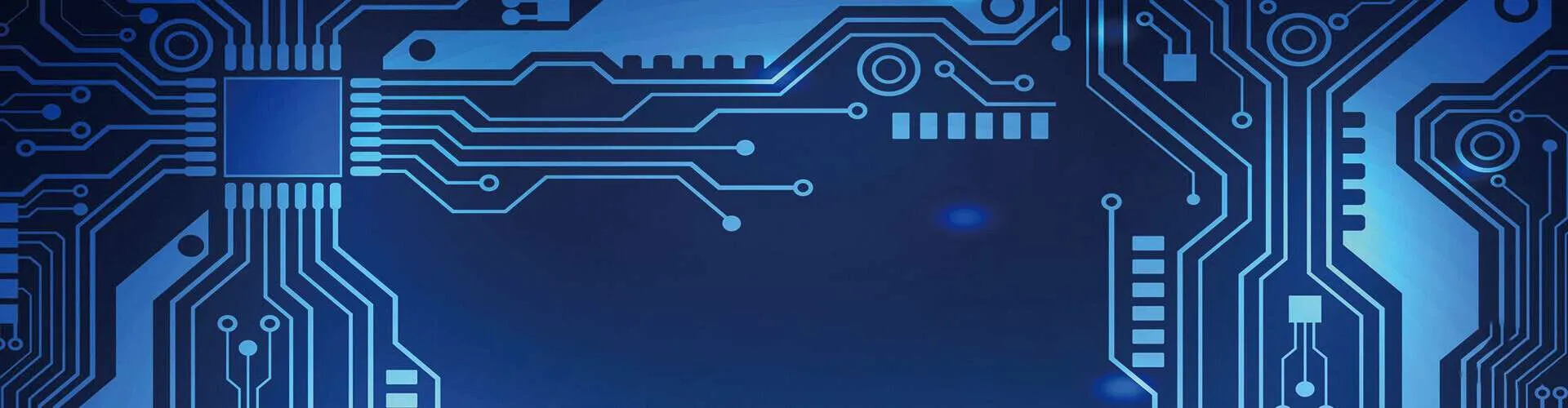
Prueba de rayos X
Domine las técnicas de prueba de rayos X para la inspección de BGA para aumentar la eficiencia, reducir los defectos y garantizar la precisión en la fabricación de productos electrónicos.
¿Qué es un BGA (Ball Grid Array)?
La prueba de rayos X se utiliza para probar BGA, QFN, etc.Matriz de rejilla de bolas (BGA) La tecnología de encapsulado es una tecnología de montaje superficial utilizada en circuitos integrados. Esta tecnología se utiliza a menudo para fijar permanentemente dispositivos como microprocesadores. El encapsulado BGA puede proporcionar más pines que otros encapsulados, como los encapsulados duales en línea o los encapsulados planos cuádruples. Toda la superficie inferior del dispositivo puede utilizarse como pines, en lugar de solo la periferia. También puede tener una longitud de cable promedio más corta que el tipo de encapsulado con periferia limitada para un mejor rendimiento a alta velocidad. El encapsulado de matriz de rejilla de bolas (BGA) es una matriz formada en la parte inferior del sustrato del encapsulado, y las bolas de soldadura se interconectan con la placa de circuito impreso (PCB) como extremo de E/S del circuito. El dispositivo encapsulado con esta tecnología es un dispositivo de montaje superficial. BGA (Ball Grid Array), también conocido como BGA, se traduce como encapsulado de matriz de contactos esféricos, y también puede traducirse como "matriz de rejilla de bolas", "matriz de bolas de soldadura en red" y "matriz esférica", etc. Es un paquete de montaje en superficie para LSI de múltiples pines, en el que los contactos esféricos se realizan en una matriz en la parte posterior del sustrato como pines y el LSI se ensambla en la parte frontal del sustrato (algunos chips BGA y extremos de los cables están en el mismo lado del sustrato).
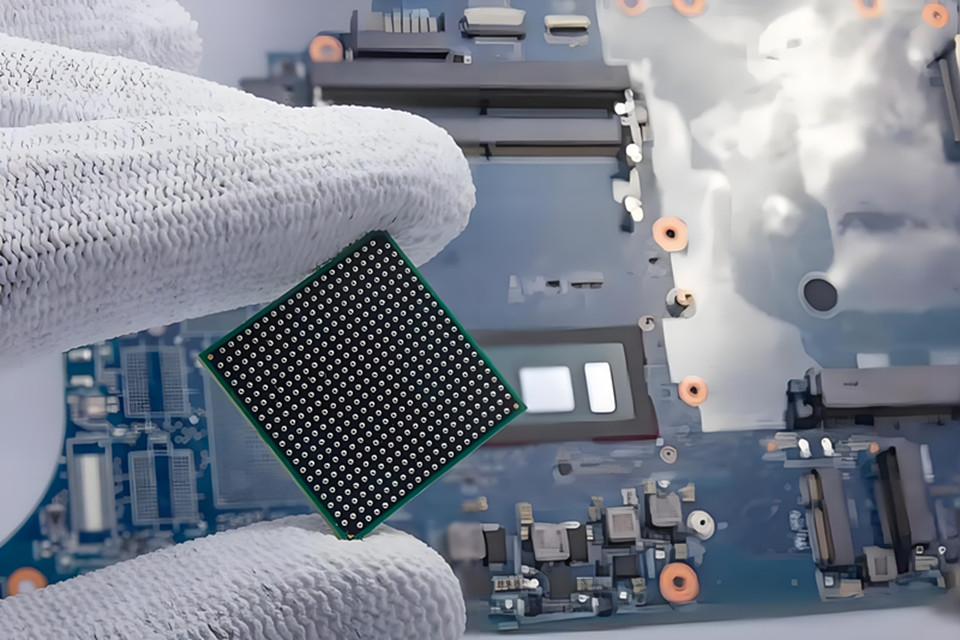
¿Cuáles son las características de la matriz de rejilla de bolas (BGA)?
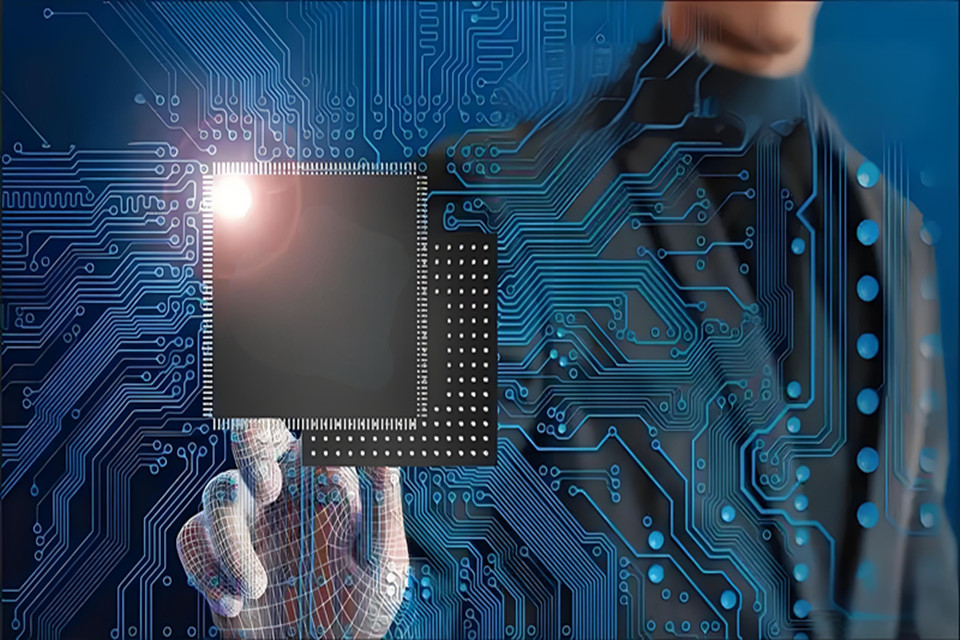
Aquí están las 10 características principales de los paquetes BGA:
- Paquete BGA alta densidad de E/S, aplicaciones de alta frecuencia primera opción
- Matriz de rejilla de bolas BGA Fuerte rendimiento de disipación de calor, estabilidad del chip garantizar
- Tecnología de encapsulado BGA parámetros parásitos bajos, retardo de transmisión de la señal minimizado
- Paquete BGA delgada y ligera, altamente integrado ahorro de espacio
- Proceso de empaquetado BGA producción automatizada, fabricación en masa bajo costo
- Paquete BGA tecnología de soldadura coplanar, fiabilidad aumentar en 30
- Paquete BGA interferencia anti-electromagnética, comunicación de alta velocidad excelente desempeño
- Paquete BGA optimización de la gestión térmica, control del consumo de energía más eficiente
- Paquete BGA Admite chips con un gran número de pines. procesador gráfico elección ideal
- Paquete BGA se utiliza ampliamente en electrónica de consumo/servidor/electrónica automotriz.
¿Qué tipo de matriz de rejilla de bolas (BGA)?
A continuación se presenta un resumen de los tipos, principales ventajas y desventajas de Embalaje BGA.
Tipos de embalaje BGA y principales ventajas
Tipos de embalaje BGA | Ventajas principales | Escenarios de aplicación típicos |
---|---|---|
Embalaje TBGA | Portador flexibleExcelente adaptación térmica, elección económica. | Electrónica de consumo solución de bajo costo |
Embalaje CBGA | Sustrato cerámico, alta hermeticidad, fuerte confiabilidad a largo plazo | Escenarios de alta confiabilidad militar/aeroespacial |
Embalaje de FCBGA | Chip invertidoAlta eficiencia de disipación de calor, antiinterferencias electromagnéticas. | Computación/servidor de alto rendimiento |
embalaje de PBGA | Sustrato de plástico, bajo costo, buena adaptación térmica | Electrónica de consumo de gama media y baja |
Embalaje FBGA | Bolas de soldadura de paso finoDiseño de alta densidad, adecuado para chips de memoria. | Controlador de almacenamiento/memoria DDR |
Embalaje de la UFBGA | Bolas de soldadura extremadamente finas, tamaño más pequeño, excelente rendimiento de alta frecuencia | Chip de comunicación 5G/IoT |
Ventajas y desventajas del paquete BGA
Ventajas principales | Características principales | Expresión de datos | Desventajas principales | Solución |
---|---|---|---|---|
Alta densidad de E/S | Aplicación de alta frecuencia | El número de pines supera 3 veces el del embalaje tradicional. | Sensible a la humedad | Embalaje a prueba de humedad + proceso de soldadura por reflujo |
Parámetros parásitos bajos | Pequeño retraso en la transmisión de señales | Estabilidad del circuito mejorada por 40% | Proceso complejo | Equipo de alta precisión + línea de producción automatizada |
Diseño ligero | Volumen reducido en 50% | Ahorre espacio en la PCB | Difícil reelaboración | Detección de rayos X + herramientas especiales de retrabajo |
Alta eficiencia de disipación de calor | El chip toca directamente el aire. | FCBGA tiene el mejor rendimiento de disipación de calor. | Diferencia de expansión térmica | Diseño de optimización de materiales de adaptación térmica |
Producción automatizada | Soldadura coplanar | Reducción de costes de 30% | Mayor costo | Compra al por mayor + optimización de procesos |
¿Cómo se suelda la matriz de rejilla de bolas (BGA) a la PCB?
A continuación se presenta un resumen de los pasos principales para soldar BGA a PCB, combinado con información sobre técnicas de soldadura de alta densidad, optimización del perfil de temperatura y más:
1. Preprocesamiento y alineación
Eliminación de humedad durante el horneado: PCB y BGA necesitan hornearse a 80-90 ℃ durante 10 a 20 horas para evitar burbujas de soldadura.
Limpieza de la superficie: retire la grasa de la almohadilla de PCB y la capa de oxidación con alcohol o agua para lavar la placa para garantizar la adhesión de la pasta de soldadura.
Alineación precisa: mediante posicionamiento óptico o alineación manual de BGA alrededor de la línea de serigrafía, lo que permite el desplazamiento 30%, el uso de autocorrección de tensión de estaño fundido.
2. Impresión y fijación de pasta de soldadura
Impresión de pasta de soldadura: aplique uniformemente pasta de soldadura (con o sin plomo) utilizando una plantilla con un grosor y aberturas que coincidan con el diámetro de la bola BGA.
Fijación de BGA: Presione ligeramente el BGA contra la PCB y evite que se desplace con la ayuda de un lápiz de succión al vacío o un fijador.
3. Control de soldadura por reflujo
Perfil de temperatura: en tres etapas: precalentamiento (calentamiento de 3-5 ℃/s), mantenimiento (penetración uniforme del calor), reflujo (pico de 220-235 ℃ de estaño fundido).
Selección de equipo: Estación de trabajo de retrabajo BGA u horno de reflujo con boquillas de aire caliente para cubrir el borde del chip y evitar el sobrecalentamiento local.
4. Enfriamiento e inspección
Enfriamiento lento: velocidad de enfriamiento natural de 3 a 10 °C/s para evitar el agrietamiento de las uniones de soldadura o la deformación de la PCB.
Verificación de calidad: fluoroscopia de rayos X de la estructura de la unión de soldadura, inspección AOI de la apariencia, prueba funcional para garantizar la conexión eléctrica.
Solución optimizada
Diseño antiinterferencias: el sustrato flexible TBGA se prefiere para escenarios de alta frecuencia para reducir la pérdida de señal.
Mejora de la disipación de calor: chip invertido FCBGA + relleno adhesivo conductor térmico para mejorar la eficiencia de disipación de calor de dispositivos de alta potencia.
¿Qué es la prueba de rayos X?
La prueba de rayos X es un método de prueba no destructivo avanzado que utiliza rayos X de baja energía para detectar la estructura interna y la calidad del objeto sin dañarlo. Este método se utiliza ampliamente en el sector industrial, especialmente en pruebas. componentes electrónicos, productos de embalaje para semiconductores, placas de circuito impreso, etc.
Detección de defectos internos no destructivos
– rayos X de baja energía PCB/semiconductor revela defectos Sin pérdida.Variedad para paquetes diversos
- DIP/SOP/QFN/BGA/Flipchip Análisis de componentes electrónicos .
Pruebas integrales por etapas
- IQC/FA/CC/GAR/I+D Flujos de trabajo Con detección de defectos automática .
Imágenes 3D avanzadas para mayor precisión
- Embalaje semcover y Placa PCB desnuda inspeccionado a nivel micro .
Importante para industrias de alto valor
- Automotriz/aeroespacial/médico sistema son válidos con estándares de cero fallos .
Detección de defectos con experiencia en costes
– Batería IGBTS/LED/iones de litio Probado para confiabilidad a largo plazo .Pruebas no comerciales de fundición de aluminio
- Integridad de los componentes metálicos verificado con mapas de densidad de rayos X .
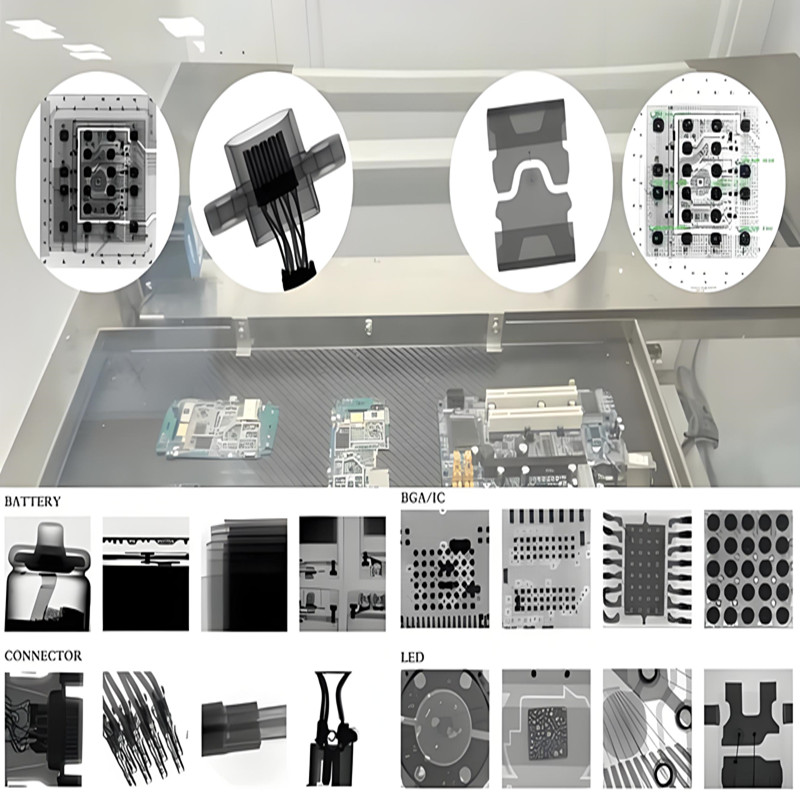
¿Cómo funciona la prueba PCBX-RAY?
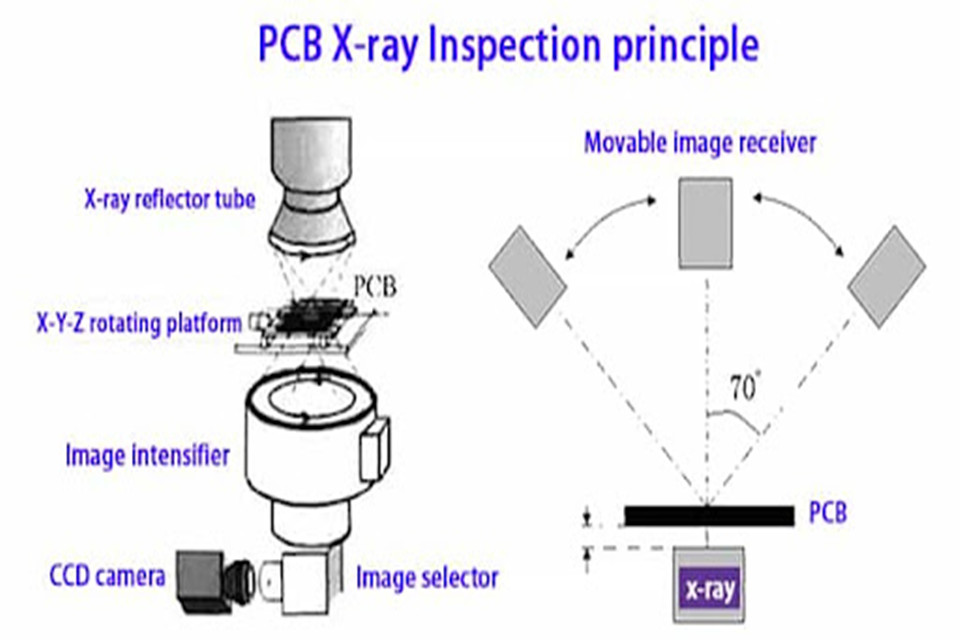
¿Cómo funciona la prueba de rayos X?
La prueba de rayos X realiza pruebas no destructivas mediante la penetración de rayos X y la diferencia de absorción de materiales. Su proceso principal es el siguiente:
Generaciones de rayos X:Las fuentes de rayos X (como los tubos de rayos X) que prueban el objeto que se está probando emiten rayos X de alta energía a alta presión.
Absorción de materiales e imágenesEl contenido de diferente densidad o espesor tiene diferentes tasas de absorción de rayos X (por ejemplo, los metales absorben más, el plástico menos). El detector capta los rayos X que entran para crear una imagen opuesta (similar a una "sombra") que refleja la estructura interna del objeto.
Identificación de defectos:El sistema de procesamiento de imágenes analiza la diferencia opuesta e identifica defectos internos (como huecos mixtos, grietas, defectos, etc.). -El equipo de alta resolución combinado con el algoritmo de IA puede marcar automáticamente los defectos y generar informes.
Panorama de aplicaciones:
- Fabricación electrónica:Encuentre bolas de soldadura BGA/QFN, juntas de soldadura PCB y estructuras de empaquetado 3D.
- Inspección industrial:Verificar piezas fundidas de metal, uniones soldadas y componentes aeroespaciales.
- Anti-falsificación:Identifique los componentes falsos comparando las diferencias estructurales internas entre los componentes reales y los falsos.
Características:
- No destructivo:No es necesario desmontar muestras para proteger productos de alto valor.
- Eficiente y preciso:La inspección de estructuras complejas se puede completar con un solo escaneo y la precisión de identificación de defectos puede alcanzar el nivel de micrones.
- Análisis multidimensional:Admite imágenes 2D y tomografía 3D (tecnología CT) para satisfacer diferentes necesidades de inspección.
Resumen comparativo de la prueba de rayos X 2D vs. la prueba de rayos X 3D
Dimensión | Prueba de rayos X 2D | Prueba de rayos X 3D |
---|---|---|
Tipo de imagen | Proyección planar | Modelo de reconstrucción 3D |
Ubicación del defecto | Proyección unidireccional, posible oclusión. | Análisis multiángulo, posicionamiento preciso de las posiciones de los defectos. |
Escenarios aplicables | Estructura sencilla, cribado rápido | Estructura compleja, detección de alta precisión. |
Costo y eficiencia | Bajo costo, rápida velocidad de detección | Alto costo, largo tiempo |
Aplicaciones típicas:
- 2D:Detección de cortocircuito en la unión de soldadura BGA, desplazamiento del pin QFP.
- 3D:Defectos de apilamiento de chips, análisis de poros a nivel micrométrico.
¿Cuáles son los beneficios clave de la prueba de rayos X?
¿Por qué elegir la prueba de rayos X para la fabricación y ensamblaje de PCB?
Aplicar defectos ocultos en PCB
- Descubrir Huecos de soldadura , Desalineaciones , y Bizing En tiempo real.
- Identificar grietas internas en PCB multicapa con precisión.
Control de calidad de PCB complejo Revolución
- Inspección PCB de alta densidad y componentes cortos eficazmente.
Copiar Asamblea de la Junta de Multi-Lear con una prueba de salario.
- Inspección PCB de alta densidad y componentes cortos eficazmente.
Reducir el riesgo de fallo del producto
- Detener fallas en el campo y daño a la reputación con detección inicial de defectos.
- Asegurar Sistemas críticos para la seguridad Estándares de confiabilidad completos.
Reducción de costes con detección temprana
- Menos tasas de desecho y costo de retrabajo mediante inspección activa.
- Adaptación Eficiencia de producción y Mejora del rendimiento .
Aumentar los límites de AOI
- Mira más allá Punto ciego AOE con visibilidad de 360° de rayos X.
- Análisis altura de la pasta de soldadura y cero por ciento automáticamente.
Prepare su producción para el futuro
- BGA/QFN/Flipchip y adaptarse a las tendencias de embalaje avanzadas.
-Milia IPC-A-610 y jedec Originalmente para cumplir con los estándares.
- BGA/QFN/Flipchip y adaptarse a las tendencias de embalaje avanzadas.
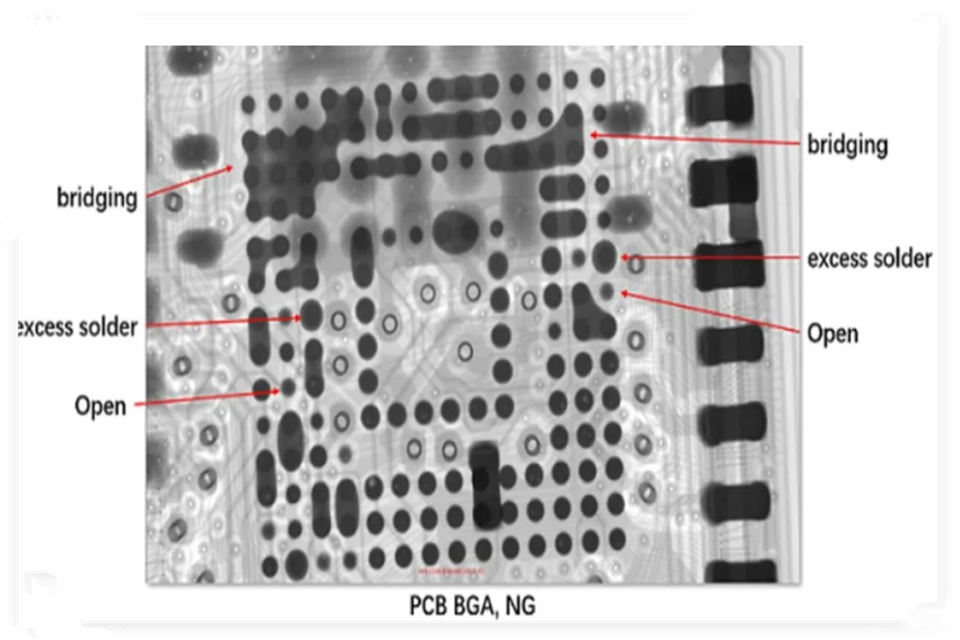
Solución a los problemas de calidad de BGA, QFN, embalajes 3D y componentes falsificados
Análisis de integridad de la bola de soldadura BGA/CSP. Verificación de la alineación del marco conductor QFN. Validación de componentes integrados.
¿Qué defectos comunes se identifican mediante la prueba de rayos X?
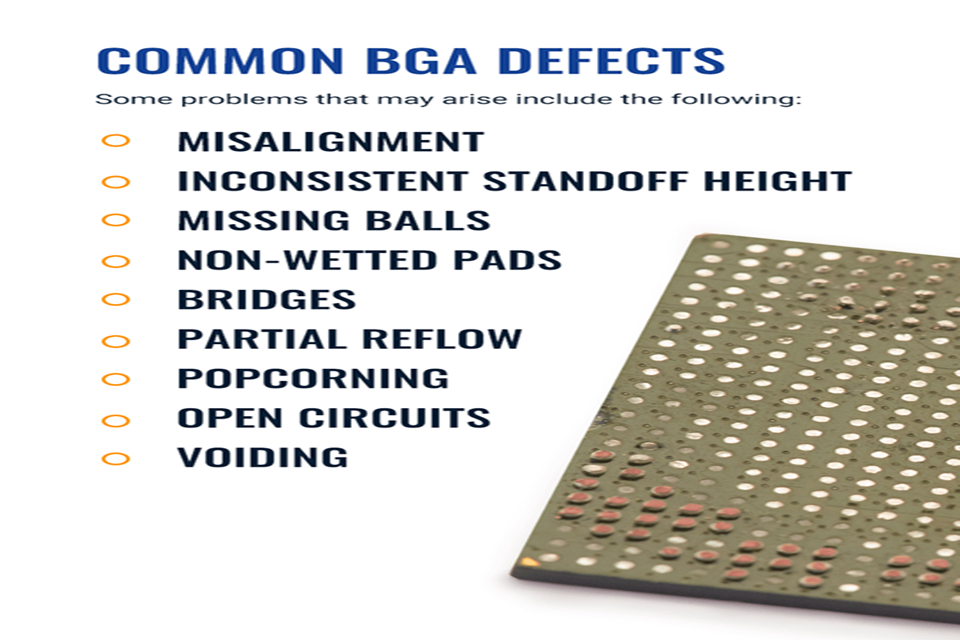
- Detectar una variedad de componentes del paquete, como BGA/QFN/Flipchip, con fuerte aplicabilidad.
- Observe la estructura del chip de apilamiento., presenta claramente el diseño interno y las líneas de encuadernación.
- Identificar con precisión los defectos del paquete, como grietas, burbujas y uniones soldadas en frío.
- Detección de área ciega AOI penetrante, compensando las limitaciones de la detección óptica, integral y eficiente.
- Analizar defectos internos de los productos, como soldadura anormal de componentes electrónicos, con fuerte visualización.
- Mide automáticamente la relación de burbujasJuicio inteligente de IA, resultados precisos y confiables.
- Cuantificar la altura de fluencia DIP, estandarizar la evaluación y mejorar la consistencia del proceso.
- Análisis de defectos mediante imágenes de alta definición, ayudar a localizar fallos y respaldar la trazabilidad de los datos.
¿Qué aplicaciones tienen las pruebas de rayos X en las distintas industrias?
1.Aeroespacial: Detectar piezas falsificadas
- Asegurar Cumplimiento de PCB de grado militar (AS9100/MIL-STD).
- Validación de sistemas de misión crítica con Imágenes de rayos X en 3D.
Automotriz: Validar sistemas de seguridad
- Inspección del controlador del airbag para riesgo de fallo cero.
- Pruebas de PCB en entornos hostiles en vehículos eléctricos y ADAS.
Electrónica de consumo: Aumente la fiabilidad
- Control de calidad de PCB de alta densidad para teléfonos inteligentes/tabletas.
- Detección de defectos en tecnología portátil en diseños compactos.
Dispositivos médicos: precisión que salva vidas
- Validación de dispositivos implantables que cumplen con la FDA.
- Inspección de la PCB del ECG/ventilador con precisión submicrónica.
Telecomunicaciones: Garantía de infraestructura 5G
- Pruebas de PCB de alta frecuencia para estaciones base 5G.
- Integridad de la placa multicapa en equipo de red.
Industrial: Soluciones para entornos hostiles
- Equipos de petróleo y gas: Rayos X para sensores submarinos.
- Validación de PCB de energía renovable (inversores solares/eólicos).
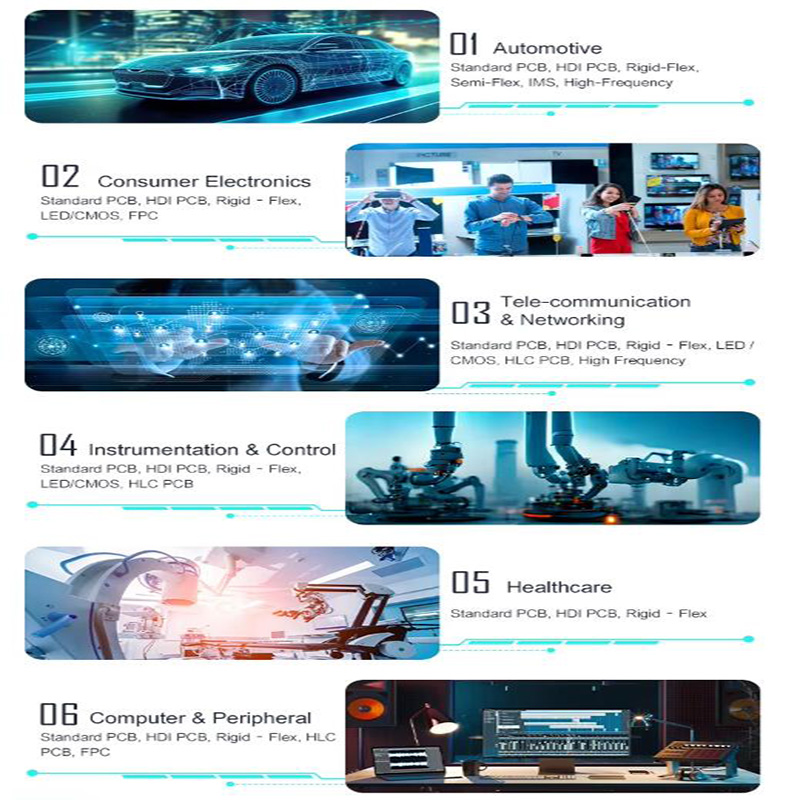
Por qué la prueba de rayos X es esencial para todas las industrias
¿Cómo elegir la prueba de rayos X adecuada?
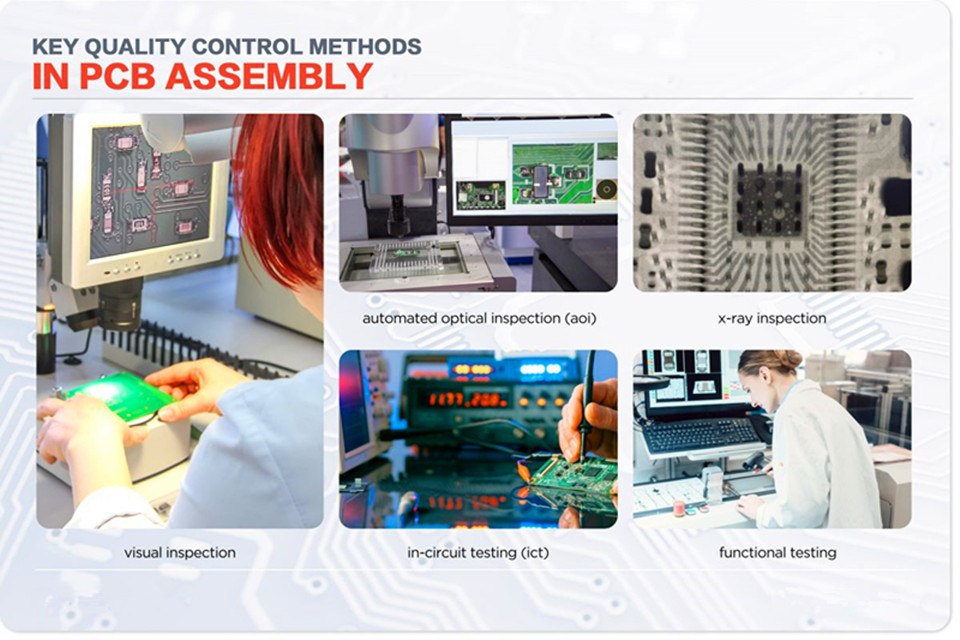
5 factores principales para elegir a tu compañero de prueba de rayos X
Garantice una fabricación orientada a la calidad con el proveedor de pruebas no destructivas y defectos precisos para productos electrónicos de misión crítica.
Cómo elegir la prueba de rayos X adecuada
1. 🔍 Resolución de submina y escaneo TC 3D
Copia de integridad de PCB multicapa con precisión <2,5 μm y análisis de cero BGA. Prioridad para la oferta del sistema:
• Tomografía automática 2.5D/3D
• Manejo de componentes de alta densidad
• Inspección certificada IPC-610
2. 🛡 Experiencia específica de la industria
Exigir verificación de grado aeroespacial y protocolo de control de calidad de vehículos motorizados. Por favor, certifique:
• Más de 10 años en pruebas de PCB médicas/5G
• Cumplimiento de las normas ISO 13485 e IATF 16949
• Bibliotecas BGA/CSP Dosha
3. ⏱ Entrega rápida y escalabilidad
Opte por el análisis el mismo día y el procesamiento por lotes de gran volumen para garantizar:
• Velocidad de escaneo del panel <5 minutos
• Soporte de línea de producción 24/7
• Lanzamiento personalizable
4. 📊 Análisis de doshas impulsado por IA
Aproveche el cálculo automático de cero% y la reacción del proceso en tiempo real. Características principales:
• Informes obedientes de IPC-7095
• Integración de datos basada en la nube
• Mapa de causas de fallas
5. 🤝 ROI - Asistencia al cliente
Socios selectos que ofrecen asesoramiento técnico 24/7 y auditoría de procesos gratuita. Prioridad:
• Servicios de representación en sitio
• Optimización de la reelaboración de BGA
• Planes de mantenimiento de vida
¿Por qué elegirnos como socio para sus pruebas de rayos X?
¿Por qué elegir SevenPCBA para la prueba de rayos X?
Experiencia técnica
- Control de calidad aeroespacial y de defensa para Imágenes de rayos X en 3D
- Análisis de dosha BGA/QFN para Tomografía computarizada 2.5D/3D
- Certificación AS9100/ISO 9001 Prueba no destructiva
Seguro de calidad
- Para detectar defectos de alta resolución en PCB y semiconductores
- Informe de grado de I+D Con clasificación automatizada de defectos
- Solución personalizada Para control de calidad de producción de alta eficiencia
Aspectos destacados del éxito del cliente
- Reducción de fallas del área 35% Aeroespacial para clientes
- 100% Cumplimiento de la FDA Para fabricantes de equipos médicos
- Prevención de reclamaciones de garantía Dosual BGA mediante identificación
- Verificación de la electrónica automotriz Con estándares de cero fallos
- Control de calidad del empaquetado de semiconductores Componentes de la red 5G
- Producción en masa con costos calificados Con información impulsada por IA
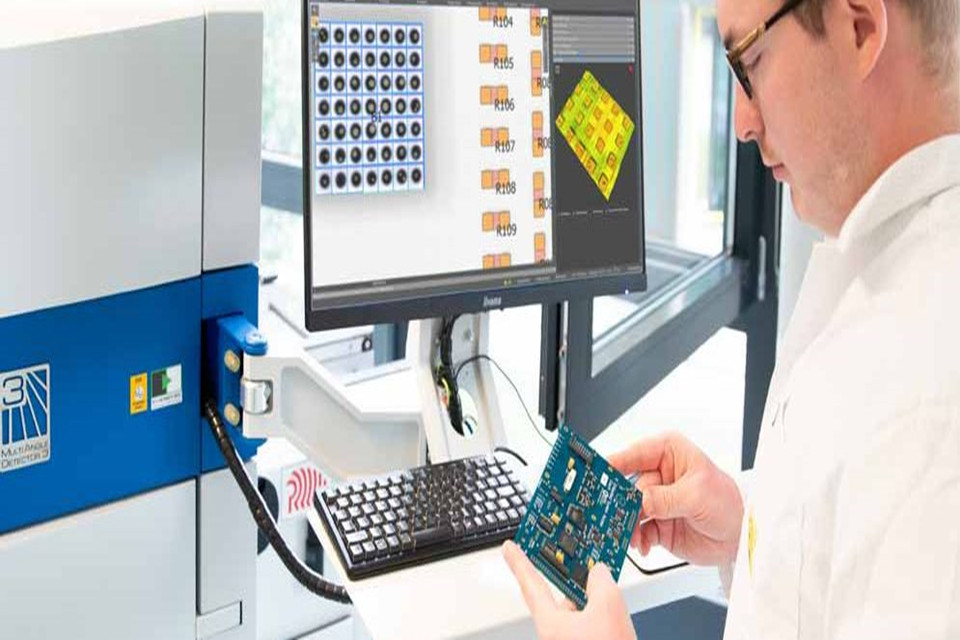