-
Xinxintian Industrial Zone, Shajing Street,Bao'an District, Shenzhen, China
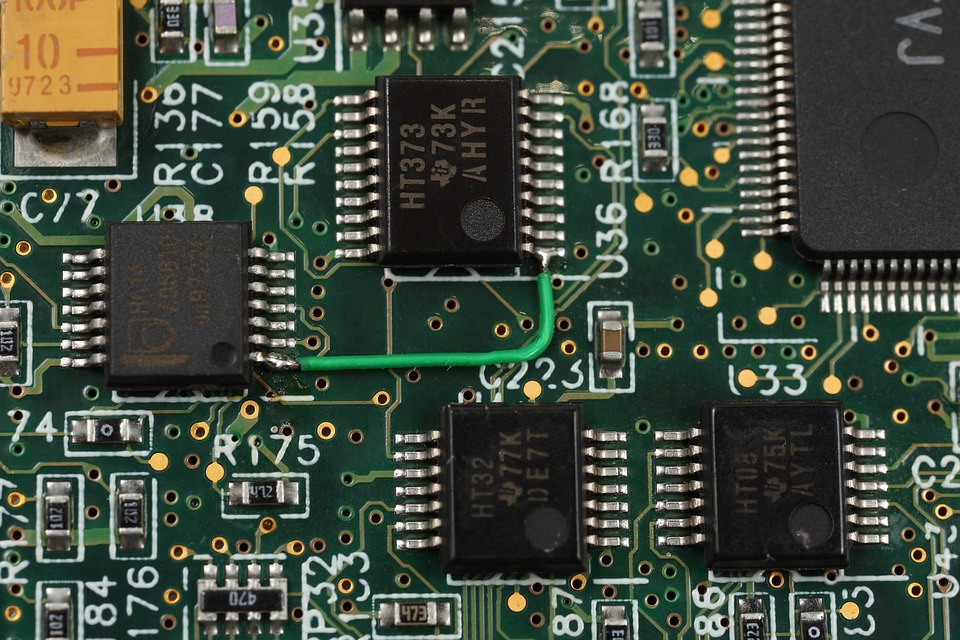
The Importance of PCB Materials: Choosing the Right Substrate for Your Project
[ad_1]
The Importance of PCB Materials: Choosing the Right Substrate for Your Project
Printed Circuit Boards (PCBs) are a crucial component in modern electronics, enabling the creation of intricate and complex electronic devices. As the foundation of these boards, the substrate material is essential in determining the performance, reliability, and lifespan of the finished product. With a multitude of options available, choosing the right substrate material can be a daunting task. This article will delve into the importance of PCB materials, highlighting the key factors to consider when selecting the perfect substrate for your project.
When it comes to PCB material selection, several key factors must be considered. These include:
- Thermal Properties: The substrate’s thermal conductivity, thermal expansion coefficient, and thermal interface material (TIM) all impact the PCB’s thermal management. A good substrate should be able to efficiently dissipate heat, reducing the risk of component overheating.
- Mechanical Properties: The substrate’s thickness, rigidity, and coefficient of thermal expansion (CTE) influence the board’s dimensional stability, solderability, and reliability. A robust substrate should be able to withstand various environmental conditions, including temperature and humidity.
- Chemical Properties: The substrate’s chemical compatibility, surface finish, and cleanliness affect the PCB’s solderability, corrosion resistance, and electromagnetic interference (EMI). A suitable substrate should be resistant to corrosion, humidity, and other environmental factors.
- ): The substrate’s dielectric properties, electrical insulation, and electromagnetic shielding impact the PCB’s signal integrity, noise reduction, and radiation resistance. A good substrate should provide sufficient insulation and shielding to prevent electrical interference.
-
Industry-Specific Requirements
Depending on the project’s specific needs, certain industries require specific substrate materials. For instance, in the aerospace industry, substrates must meet extreme temperature and corrosive environment requirements. In contrast, consumer electronics may prioritize aesthetics, durability, and affordability.
Commonly Used Substrates
Several popular substrate materials are widely used in PCB manufacturing. Some of the most common include:
- Olefin (FR4): A cost-effective, flame-resistant option with good thermal conductivity, commonly used in consumer electronics and industrial applications.
- Polyimide (PI): A high-temperature-resistant, high-insulating material with low CTE, often used in aerospace, automotive, and computing applications.
- Rogers (FR5): A high-frequency, high-dielectric material with low loss tangent, typically used in radiofrequency (RF) and microwave applications.
- BT (FR5): A high-temperature-resistant, high-insulating material with good thermal conductivity, commonly used in automotive, industrial, and aerospace industries.
Lessons Learned
When selecting a substrate material, it’s essential to consider the specific requirements of your project, including thermal, mechanical, chemical, and electrical properties. By balancing these factors, you can ensure the optimal performance and reliability of your PCB. Remember:
- Evaluate the application’s specific requirements: Consider the environmental conditions, component selection, and industry regulations to determine the most suitable substrate material.
- Benchmark and compare options: Analyze the performance, cost, and limitations of various substrate materials to make an informed decision.
- Consult experts and manufacturers: Leverage the expertise of PCB manufacturers, suppliers, and industry professionals to gain valuable insights and avoid common pitfalls.
Conclusion
Choosing the right PCB substrate material is a critical step in the design and manufacturing process. By understanding the key factors, such as thermal, mechanical, chemical, and electrical properties, you can select a substrate that meets your project’s specific requirements. Remember to evaluate application-specific needs, benchmark and compare options, and consult experts to ensure the optimal performance and reliability of your printed circuit board.
FAQs
Q: What is the most common substrate material used in PCB manufacturing?
A: Olefin (FR4) is the most widely used substrate material, known for its cost-effectiveness and good thermal conductivity.
Q: What is the difference between FR4 and FR5?
A: FR4 (Olefin) has a higher thermal conductivity and CTE than FR5 (Rogers), making it more suitable for consumer electronics, while FR5 is better suited for high-frequency applications.
Q: Can I use a single substrate material for all my projects?
A: No, each project has unique requirements; it’s essential to evaluate the specific needs of your application before selecting a substrate material.
Q: Can I use a substrate material that meets the requirements of one industry for another?
A: No, industry-specific substrates may not meet the requirements of another industry; it’s crucial to select a substrate that complies with the regulations and environmental conditions of the intended application.
[ad_2]