-
Industriegebiet Xinxintian, Shajing-Straße, Bezirk Bao'an, Shenzhen, China
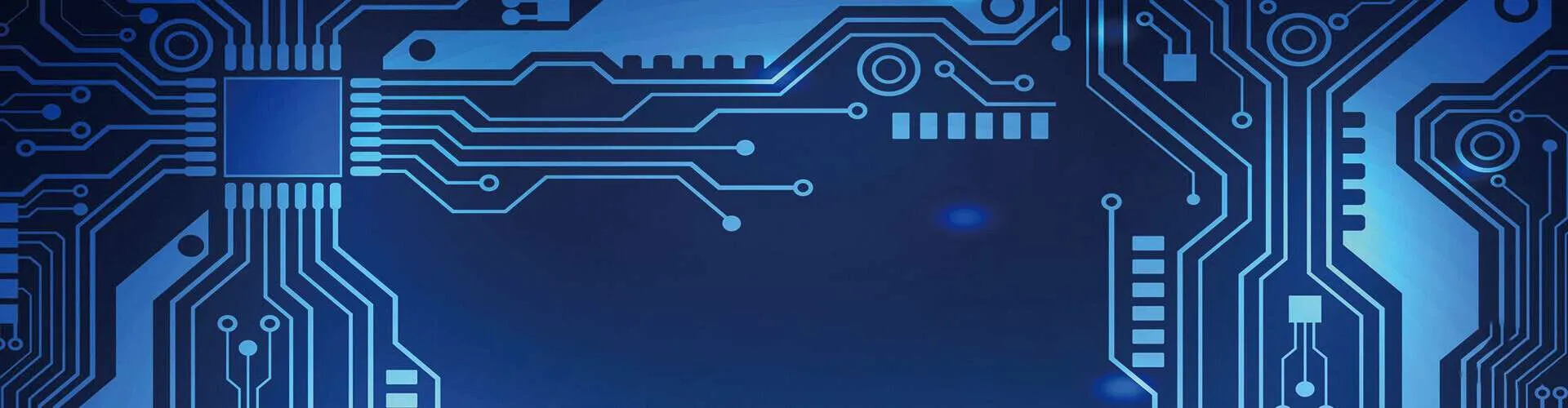
Kastenmontage
Meistern Sie die Kartonmontage mit unserer Schritt-für-Schritt-Anleitung, um die Produktion zu optimieren, Kosten zu senken und die Qualität zu verbessern
Was ist eine Box-Baugruppe?
Mit der rasanten Entwicklung intelligenter Hardware und elektronischer Geräte ist die modulare elektromechanische Montage (Box Assembly) als zentrale Technologie im Bereich der Systemintegration zu einem wichtigen Bindeglied in der Herstellung elektronischer Produkte geworden. Dieser präzise Montageprozess umfasst nicht nur die traditionelle Leiterplattenmontage (PCB), sondern integriert auch Komponenten wie Kabel, Sensoren und mechanische Strukturen. Durch die mechatronische Integration entstehen einsatzbereite Endprodukte, die die Produktleistung und -zuverlässigkeit deutlich verbessern.
PCB-Box-Baugruppe
Meistern Sie die Kartonmontage mit unserer Schritt-für-Schritt-Anleitung, um die Produktion zu optimieren, Kosten zu senken und die Qualität zu verbessern
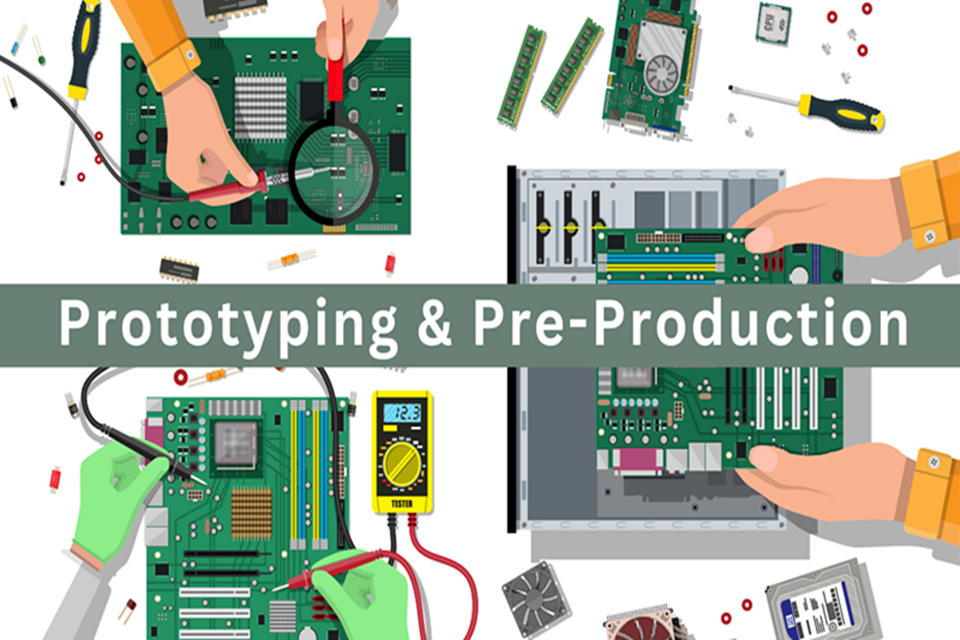
Welche Informationen werden für die PCB-Box-Montage benötigt?
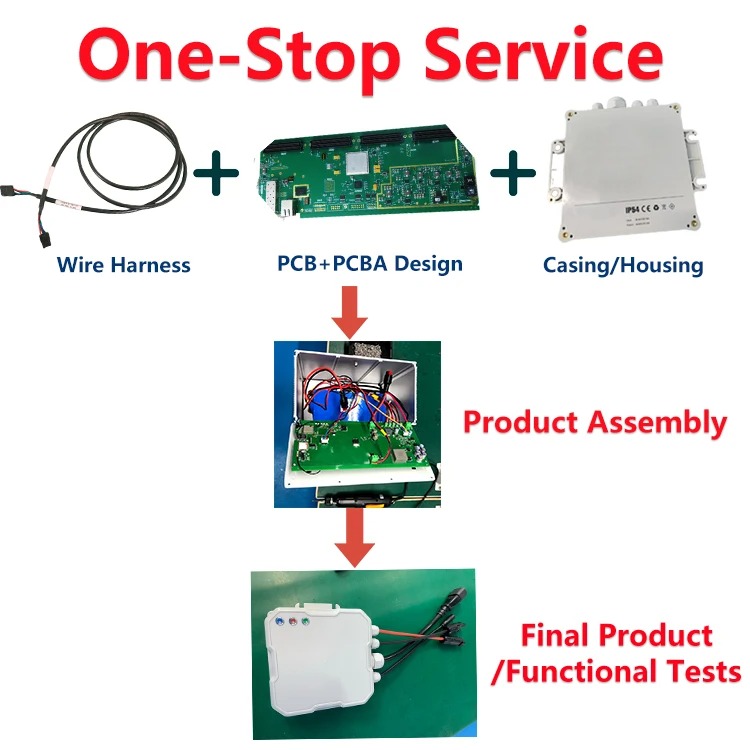
Kartonmontage-Experte an Ihrer Seite
Zehn Dinge, die vor der Boxmontage vorbereitet werden sollten
1. Die Materialliste (BOM): Teilenummer, Herstellername, alternative Komponenten.
2.Gerber-Datei (Leiterplattendesign):Bohrschema, Lötstoppmaske und Siebdruckmarkierung.
3. PCB-Bestückungszeichnung (Bestückungsdiagramm):Die Leiterplattenbestückungszeichnung (Bestückungsdiagramm) enthält die Identifizierung der Komponentenpolarität und das mechanische Positionierungsloch
4.Shell-Spezifikation (Schutzhüllenparameter):Maßtoleranz, Anforderungen an die Wärmeableitung, störungsfreies Design.
5.PCBA-Testdatei, die zur Funktionsüberprüfung verwendet wird:elektrische Leistungsindikatoren und Alterungstestparameter.
6. Die Konformitätsbescheinigungsdokumente:Dabei handelt es sich um Industriequalifikationszertifikate, die eine RoHS-Zertifizierung und einen EMV-Testbericht umfassen.
7.3D-Modelldatei (Strukturüberprüfungsdaten):Interferenzanalyse der Box-Montage, Wärmeableitungssimulation
8.Materialparametertabelle (Beschreibung der Substrateigenschaften):Dielektrizitätskonstante, Wärmeausdehnungskoeffizient, Temperaturbeständigkeit
9. Verpackungs- und Transporthinweise (Antistatik-Anforderungen):Erdbebensicherheit, Feuchtigkeitskontrolle, Antioxidationsbehandlung
10.Die Kundennachfragetabelle:Darin werden kundenspezifische Serviceleistungen beschrieben, einschließlich des Oberflächenbehandlungsprozesses und der Positionierung des Siebdrucklogos.
Welcher Schlüsselprozess ist der Kartonzusammenbau?
Zehn Schlüsselprozesse für die PCB-Box-Montage, sie helfen, die Produktion klarer zu gestalten
1.Überprüfung des Kastenstrukturdesigns:3D-Modellanpassung, EMV-Zirkulationssimulation
2.Hauptformöffnung:Materialauswahl und Antimigration, Toleranzausgleichsschema
3.Vorinstallation und Debuggen der Box:mechanische Positionierungskalibrierung, Wärmeableitungskanalerkennung
4.Leiterplattenschweißmontage:SMT-Reflow-Löten, Verstärkung der BGA-Ballpflanzung
5.Integration des Wärmespendermoduls:Wärmeleitfähigkeit von Flüssigmetallen, feineres Laserschweißen
6.Installation der elektromagnetischen Abdeckung:Mehrpunkt-Erdungsbehandlung, HF-Lecktest
7.Schnittstellensonden-Customizer Wasserdicht:Strukturverschachtelung, Anti-Narren-Bakkal-Design
8.Konforme Proof-Beschichtung:Verfahren: Nano-hydrophobe Beschichtung, Salzsprüh-Konservierungsbehandlung
9.Kompletter Maschinenverbindungstest:Fallaufprallprüfung, Hoch- und Niedertemperaturzyklus
10.Antistatische Verpackung:Vakuumverpackung aus Aluminiumfolie, druckfeste EPE-Beschichtung
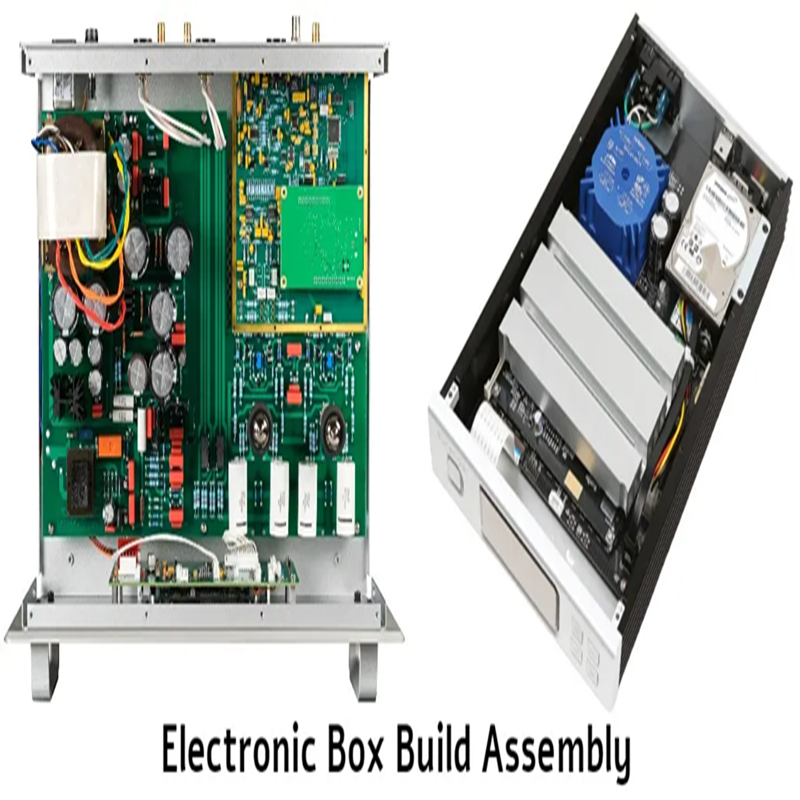
Welche Faktoren sind für eine erfolgreiche Kartonmontage wichtig?
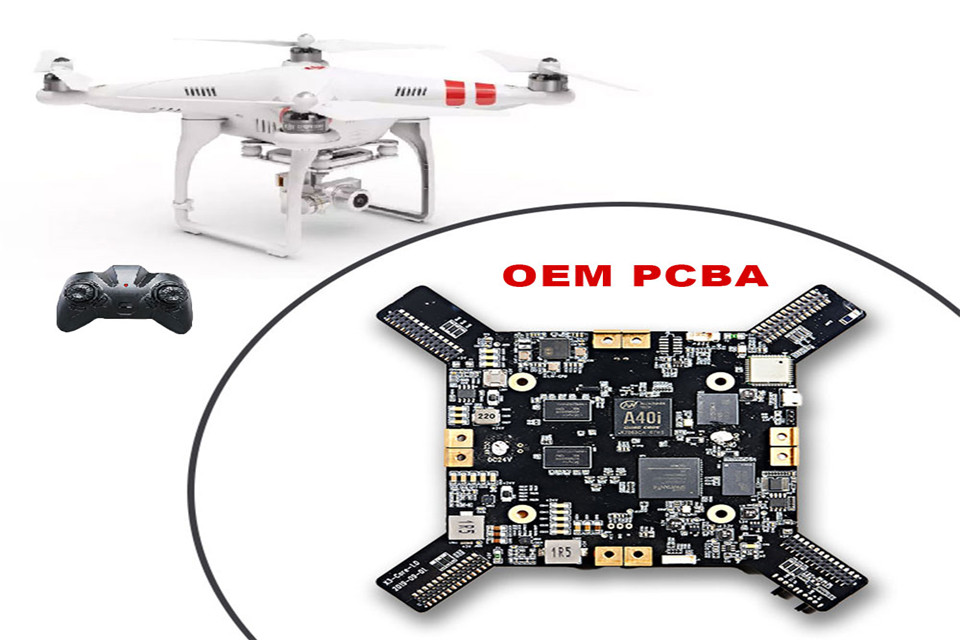
Sechs Schlüsselfaktoren für eine erfolgreiche PCB-Box-Montage
Sie sind bis zum Abschluss zwischen OEM- und EMS-Unternehmen (Electronics Manufacturing Services) miteinander verknüpft. Sie sorgen für eine reibungslosere Produktion und steigern die Wettbewerbsfähigkeit Ihres Unternehmens!
- Vollständige Konstruktionsunterlagen: Bereitstellung von Spezifikationsdokumenten und einer genauen Stückliste
- Präzises Komponentenlayout: Geräteabstand und symmetrische Verteilung optimieren.
- DFM-Herstellbarkeit: Löt- und Montagerisiken schon im Vorfeld vermeiden.
- Effizientes Wärmeableitungsdesign: Sorgen Sie für eine ausgewogene Anordnung der Wärmequellen und Wärmeableitungswege.
- Strenge Prozesskontrolle: Standardisierung der bleifreien/bleihaltigen Prozesstrennung.
- Zuverlässige Lötqualität: Verbessertes Pad-Design und Polaritätsmarkierung.
Welche Herausforderungen gibt es bei der Kartonmontage und welche Lösung gibt es?
6 Herausforderungen und Lösungen für die Leiterplattenmontage
- Herausforderung 1: Falsche Materialauswahl → Antwort: Strenge Materialprüfung, um sicherzustellen, dass die Leistung dem Standard entspricht (z. B. flexible PCB-Materialien, Materialien mit hoher Wärmeleitfähigkeit).
- Herausforderung 2: Häufige Lötfehler → Antwort: Lötprozessparameter optimieren und einführen Reflow-/Wellenlöttechnologie.
- Herausforderung 3: Abweichung in der strukturellen Ausrichtung → Antwort: Annahme von hochpräzise Ausrichtgeräte zu verbessern Präzision bei der Mehrschicht-Leiterplattenmontage.
- Herausforderung 4: Unzureichende Umweltkontrolle → Antwort: Implement Temperatur- und Feuchtigkeitskontrolle und antistatische Arbeitsplätze ausstatten (Antistatikmaßnahmen).
- Herausforderung 5: Fehlende Testvalidierung → Bewältigung: Implementierung vollständiger Inspektionsprozess, kombinierter Falltest, Prüfung der elektromagnetischen Verträglichkeit.
- Herausforderung 6: Kosten- und Effizienzungleichgewicht → Antwort: Optimieren Sie die Schlanker Fertigungsprozess und Redundanzen zu reduzieren (Automatisierte Montagelösung).
Durch die Lösung dieser Kernprobleme können wir die Ausbeute und Zuverlässigkeit von PCB-Gehäusebaugruppe, anziehen Unternehmen der Elektronikfertigung Beratungskooperation und fördern die Konversionsrate von Leiterplattenmontagedienste.
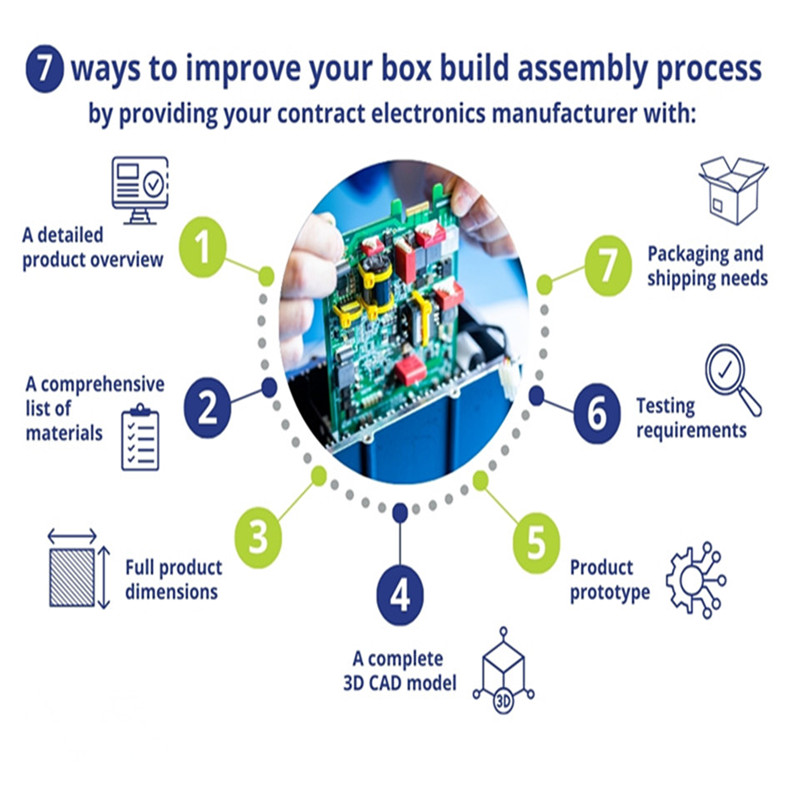
Warum die USA als Partner für die Kartonmontage?
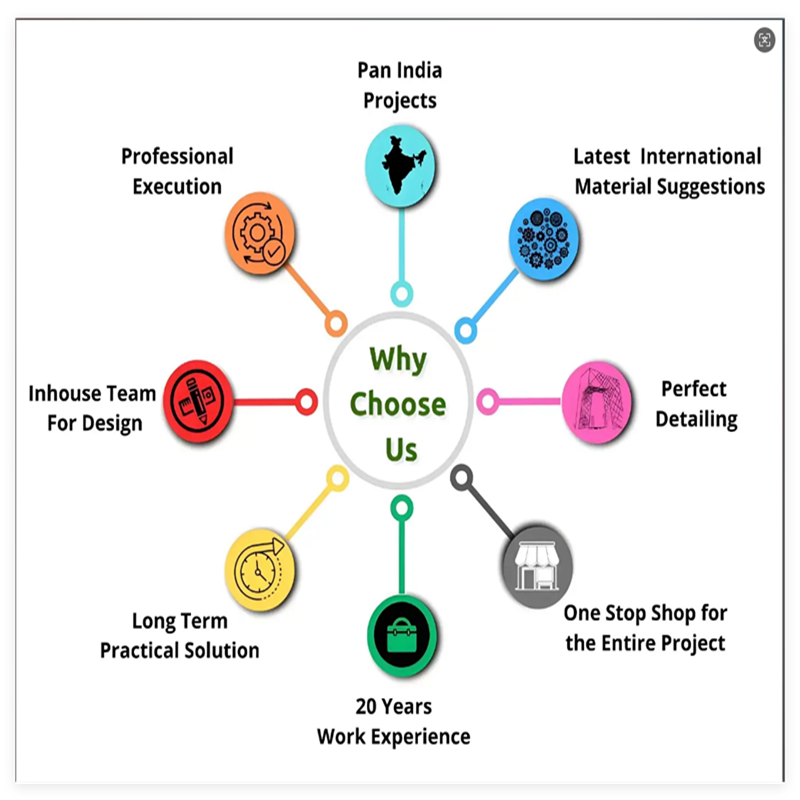
6 wichtige Gründe, sich für unseren Kartonmontageservice zu entscheiden
- Optimierung der gesamten Lebenszykluskosten: Reduzieren Sie die Gesamtkosten und steigern Sie die Effizienz.
- Präzises Qualitätskontrollsystem: Strenge Tests zur Gewährleistung der Produktstabilität (Qualitätsservice ohne Fehler).
- Schnellliefergarantie: Intelligentes Lagersystem zur Verkürzung des Produktionszyklus (Effiziente Montagelieferung).
- Professioneller technischer Support: bieten Integriertes PCB- und Gehäusedesign um komplexe Anforderungen zu lösen.
- Maßgeschneiderte, flexible Produktion: Anpassung kleiner Chargen an die Nachfrage der Massenproduktion (Personalisierte Lösungen für die elektronische Montage).
- Garantie der Einhaltung von Umweltvorschriften: Erfüllen Sie RoHS und andere Standards, um rechtliche Risiken zu vermeiden (Umweltfreundliche Fertigungsdienstleistungen).