-
Xinxintian Industrial Zone, Shajing Street,Bao'an District, Shenzhen, China
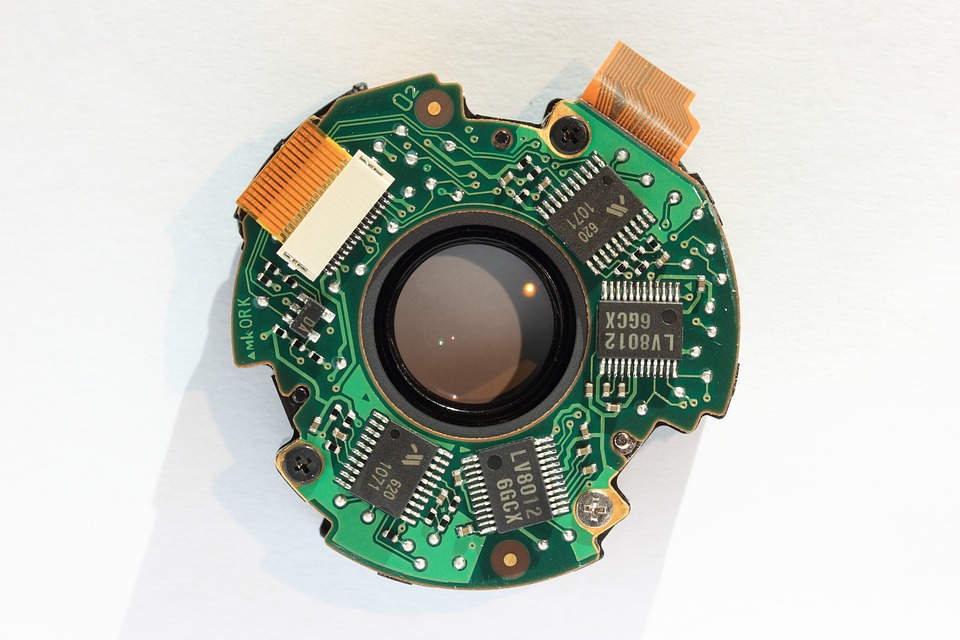
PCB Assembly for Industrial Control Systems: Ensuring Dependable Performance in Harsh Environments
[ad_1]
PCB Assembly for Industrial Control Systems: Ensuring Dependable Performance in Harsh Environments
Industrial control systems are designed to operate in some of the harshest environments imaginable, with high temperatures, high-pressure, and humid conditions that push the limits of even the most reliable electronic components. PCB (Printed Circuit Board) assembly plays a critical role in ensuring the reliable performance of these systems, and it’s essential to choose the right components, materials, and assembly techniques to ensure they can withstand the rigors of the industrial environment.
The Importance of Reliability in Industrial Control Systems
Industrial control systems are responsible for monitoring and controlling a wide range of processes, from manufacturing lines to oil refineries, power plants, and other critical infrastructure. These systems are critical to the smooth operation of the plant, and downtime can result in significant financial losses and environmental damage. For this reason, reliability is paramount in the design and assembly of these systems.
PCB assembly is a critical component of industrial control systems, and its reliability is closely tied to the performance of the overall system. PCBs are responsible for processing data, controlling electrical signals, and regulating the flow of energy, and any malfunctions can have a direct impact on the system’s performance and safety.
Challenges in PCB Assembly for Industrial Control Systems
PCB assembly for industrial control systems presents several challenges, including:
Extreme temperatures: Industrial control systems often operate in environments with temperatures above 100°C, which can cause components to degrade and malfunction.
High humidity: Humid environments can cause moisture to seep into the PCB, leading to corrosion and electrical shorts.
Vibration and shock: Industrial control systems are often exposed to heavy machinery and vibration, which can cause components to fail or malfunction.
Electromagnetic interference (EMI): Industrial control systems are often located near sources of EMI, which can cause electrical signals to be degraded or disrupted.
To overcome these challenges, PCB manufacturers must use specialized components and materials, such as:
High-temperature-resistant components: Resistors, capacitors, and inductors designed to operate in extreme temperatures.
Moisture-resistant materials: PCBs constructed with materials that can withstand moisture and humidity, such as epoxy or PTFE (polytetrafluoethylene) coatings.
Vibration-resistant components: Solder joints and components designed to resist vibration and shock, such as surface-mount technology (SMT) components.
EMI shielding: PCBs designed with EMI shielding to prevent interference, such as conductive materials like copper or aluminum.
Best Practices for PCB Assembly in Industrial Control Systems
To ensure the reliability and performance of PCBs in industrial control systems, it’s essential to follow best practices for assembly, including:
Proper component placement: Ensuring components are securely fastened to the PCB to prevent vibration-induced damage.
Surface preparation: Cleaning and preparing the PCB surface to ensure a strong bonding process and prevent contamination.
Soldering and joining: Using specialized soldering and joining techniques to ensure secure and reliable connections.
Quality control: Conducting rigorous testing and inspection to ensure the PCB meets the required standards for performance and reliability.
Conclusion
In conclusion, PCB assembly is a critical component of industrial control systems, and its reliability is essential to the performance of the overall system. By choosing the right components, materials, and assembly techniques, PCB manufacturers can ensure their products meet the demands of the harsh industrial environment. By following best practices for assembly, including proper component placement, surface preparation, soldering and joining, and quality control, PCBs can be designed and assembled to withstand the rigors of the industrial environment and provide reliable performance and reduced downtime.
FAQs
Q: What are the most common challenges in PCB assembly for industrial control systems?
A: The most common challenges include extreme temperatures, high humidity, vibration and shock, and electromagnetic interference (EMI).
Q: How can I ensure the reliability of PCBs in industrial control systems?
A: By choosing the right components, materials, and assembly techniques, ensuring proper component placement, surface preparation, soldering and joining, and conductng rigorous testing and inspection.
Q: What are some of the specialized components and materials used in PCB assembly for industrial control systems?
A: High-temperature-resistant components, moisture-resistant materials, vibration-resistant components, and EMI shielding materials.
[ad_2]